Supply Chain Woes Impact Building Envelope Projects
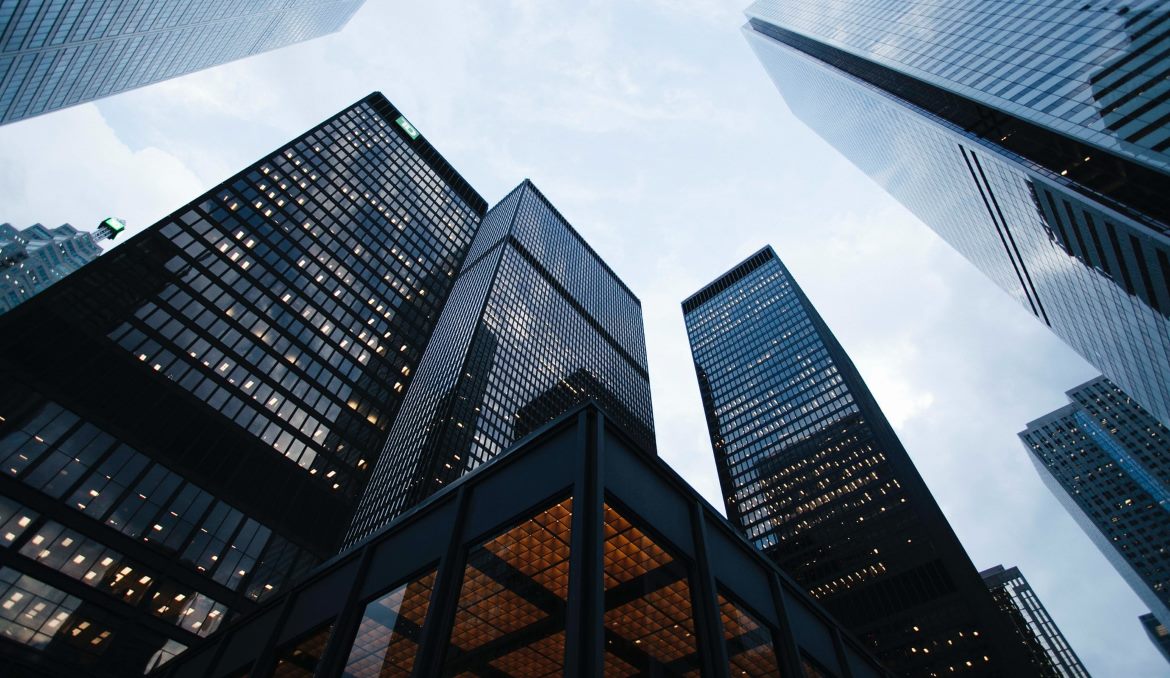
Photo courtesy of Sean Pollock via Unsplash.
Commercial building envelope projects are crucial for overall success. The building envelope comprises components such as exterior walls, roofs, doors and the foundation, so it plays a vital role in protecting the structure against harsh environmental elements. It also promotes temperature retention and soundproofing. Given its importance, it’s easy to see why supply chain shortages could significantly impact commercial project timelines.
Here’s a closer look at the extent of the problem and, more importantly, how experts can adapt to the issue.
Seek Joint Partnerships With Those Who Have Supplier Connections
The Marcum Commercial Construction Index profiled the sector for the first quarter of 2022. The company’s data confirmed that although residential construction has maintained momentum, that’s not the case with nonresidential builds. Such projects showed a 5.6% year-over-year spending boost.
However, people involved with the report said the figure actually represents a setback due to inflation. Moreover, investment in nonresidential construction showed a 0.9% decline in the first quarter of 2022, indicating a trend that has persisted for nine of the last 10 quarters.
When commenting on the research, Joseph Natarelli, the construction leader at Marcum, said contractors are pursuing various creative strategies to deal with supply chain issues. One emerging coping strategy is to enter into partnerships with individuals or groups that have insider connections with suppliers. This collaboration can make procurement easier.
Such joint ventures may also extend to labor force needs. In addition to the challenges posed by supply shortages, a lack of workers could also delay building envelope progress.
Thorough Planning Is Essential During These Challenging Times
One of the most practical ways for experts to adapt is to adjust their usual time frames. Supply chain shortages typically lengthen the time it takes to get the desired supplies. They may even necessitate using alternative materials or methods. Some events cause long-term supply chain shortages, too.
Texas experienced unprecedented cold weather in 2021. The freezing conditions interfered with the production of methylene diphenyl diisocyanate, a key chemical used in roofing insulation. This trend has caused some decision-makers to opt for roof restorations rather than replacements.
However, designers and clients must prepare for longer wait times when building envelope projects require new roofs or other critical materials. Many companies order their goods several months in advance, so there’s little leeway for last-minute decisions.
Design experts may also want to consider working with suppliers that use technological solutions to manage supply chain shortcomings. The Internet of Things (IoT) and artificial intelligence (AI) can help suppliers track trends and respond faster. Then, contractors and their clients are less likely to experience prolonged adverse effects.
Leverage Long-Term Supplier Relationships
AEC professionals with a presence in multiple countries know the importance of understanding how regulations differ across nations or regions. For example, Euroclass is the fire safety standard across Europe, but the United States uses different metrics for combustibility and facade materials. However, materials produced elsewhere may meet or exceed standards for commercial buildings in an area experiencing acute shortages.
It’s always useful to rely on the value that long-term supplier relationships can bring. Consider a case where a commercial contractor has a solid history of consistently placing orders and paying invoices on time. A supplier is arguably more likely to fulfill the needs of that client before addressing those from parties that have not yet proven themselves so reliable.
Turner Construction is one of the leading firms in the industry. Its CEO revealed that the company has depended on a supply chain management service to ease some procurement difficulties. It has also taken advantage of existing supplier relationships in Europe and China to improve planning for its domestic projects.
Searching for supplies through international relationships is not a sure bet. As of August 2021, a record 15% of European Union contractors reported materials shortages. More recently, in the spring of 2022, people familiar with the Irish commercial construction market reported significant price volatility for goods such as foundation materials and steel due to inflation and the Russian invasion of Ukraine. Many contractors there managed risks through contractual agreements that had clients bearing most of the potential inflation-related costs.
Utilize On- or Off-Site Storage Opportunities
Ordering building envelope materials substantially sooner than usual can help commercial contracts minimize the effects of some supply chain challenges. Construction industry analysts across the United States say one of the most noticeable changes brought about by materials shortages relates to the stockpiling of materials on job sites.
Contractors generally use shipping containers, tarps and off-site storage locations to manage the goods they buy ahead of time. Such solutions have associated costs. However, the people familiar with this strategy say the expenses are usually less than those connected to the problem of not having materials available when needed.
Running out of critical materials could easily add months to a project’s total timeline. Related concerns crop up when workforces can’t continue their tasks because the supplies aren’t there. One construction executive based in California reported that lead times can be as long as a year for aluminum windows. Lead times have also extended into 2023 for open bar joists.
Building professionals aren’t having an easy time sourcing warehouse space for their stockpiled goods, though. In this case, thinking creatively can pay off. Some construction professionals have connected with big-box retailers to see if they’re willing to provide some space. Others are even building their own temporary warehouses instead of looking for existing ones with room available.
Stockpiling materials is not an option for every commercial contractor. However, industry professionals who strongly consider it should be aware of all the potential variables. For example, a supplier may give bulk discounts, making it appealing to purchase the building envelope materials for numerous projects with one order. However, the contractor in the arrangement might not have the on-site space to store everything. Companies must then consider the costs of transporting materials to the site.
Flexibility Is a Must
Many commercial construction experts agree that the supply chain challenges mentioned here and elsewhere won’t be resolved anytime soon. People at contracting companies affected by the problem should remain as flexible as possible while searching for viable solutions.
Now is not the time to lean on a “business as usual” mindset. It’s essential to continually explore new ways of procuring supplies, even if it means company representatives go outside their comfort zones or beyond what they previously tried.