How Tariffs on Aluminum & Steel Will Impact Architects & Specifiers
An interview with Brent A. Schipper AIA, LEED AP, Founding Principal, ASK Studio
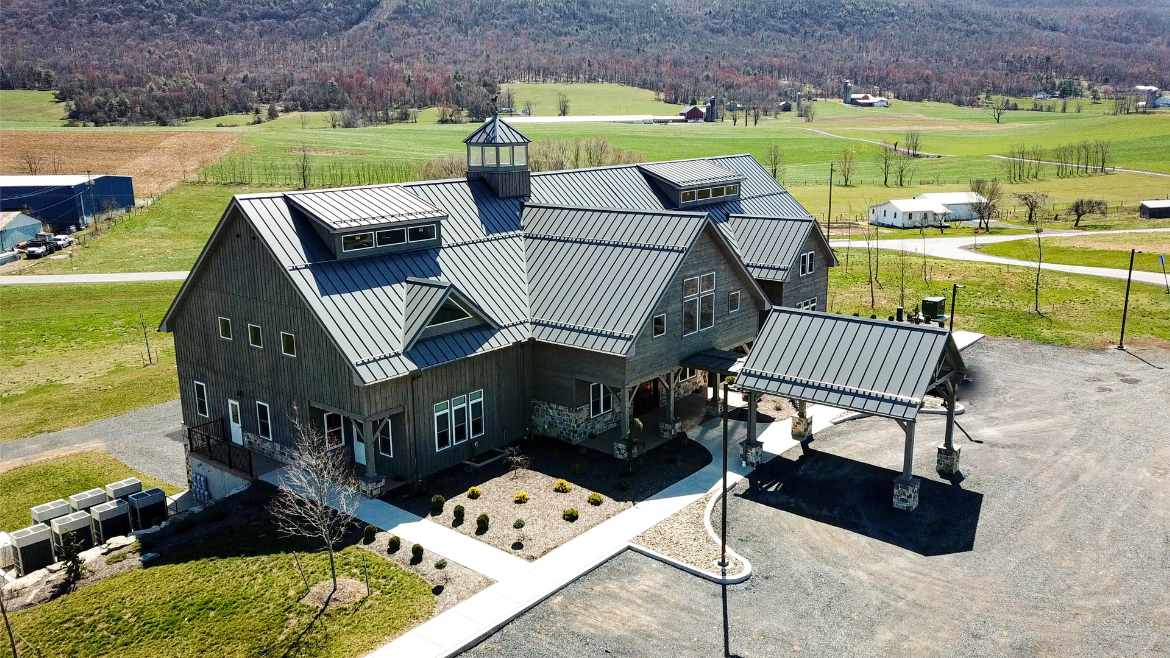
Central Pennsylvania Health Clinic in Belleville, PA. Photo courtesy of Fisher's Roofing, Loysville, PA.
The costs of construction materials continue to remain steadily high, fueled in part by tariffs on steel and aluminum. Furthermore, ongoing market uncertainty often causes prices to surge even before the full impact of tariffs takes effect, a major concern for architects and specifiers. For firms like ASK Studio, a midwestern-based architectural firm, navigating this uncertainty requires a defensive strategy focused on materials less susceptible to the impact of tariffs.
As Brent A. Schipper AIA, LEED AP, Founding Principal at ASK Studio and long-time advisor to METALCON – the metal construction and design industry’s leading event for education and innovation – explains, “Our firm has always championed the benefits of steel, due to its durability, 98% recyclability, fire resilience and long-term performance, but we can’t afford to design with materials that could lead to cost overages or require redesigns down the line. While tariffs are affecting many building products, steel is particularly vulnerable due to its high reliance on foreign sources. We’re now exploring materials such as curtainwall systems, masonry and even wood, which are less susceptible to tariff-related price increases.”
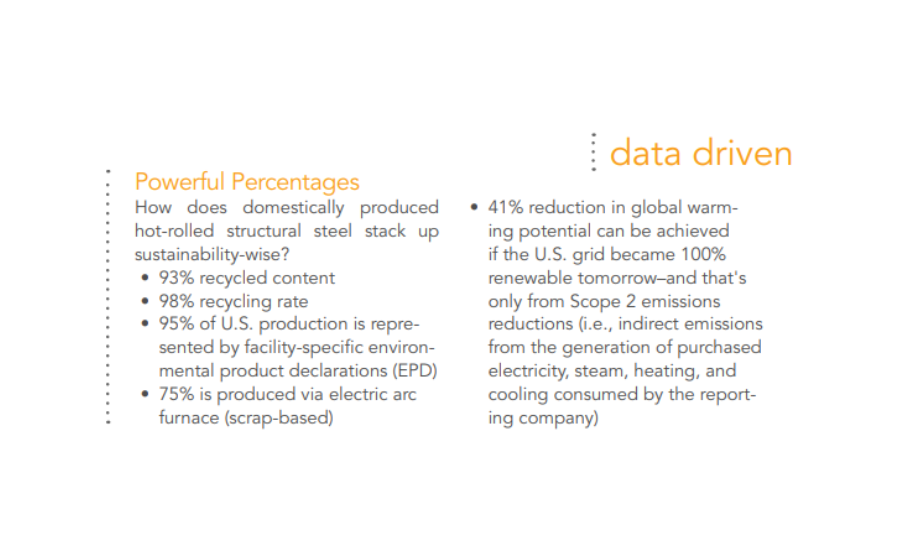
The Challenges of Material Costs
Just the talk of steel and aluminum tariffs have already manifested in missed project budgets and lost time for architects. With higher material costs on the horizon, architects are focusing on minimizing the risks of exceeding project budgets. Firms are considering construction systems with less steel density per square foot, such as concrete structures, heavy timber and traditional wood framing. These alternatives are perceived to offer potential cost savings.
However, the challenges are many. Schipper points out that while wood may seem like a viable alternative, it too is facing the effects of tariffs. Additionally, the labor market for concrete construction is already stretched thin, and the potential ramifications of changing immigration policies could further impact the workforce shortage.
Another concern is aluminum, a key material in many commercial buildings. Schipper notes that approximately 75% of commercial buildings utilize aluminum windows or glazing systems, and there are few viable substitutes. Budget-friendly alternatives are hard to come by, further complicating the situation for architects trying to stay within budget.
An Economic Perspective on Tariffs
Brent turns to his son, Tyler Schipper, an economics professor at the University of St. Thomas in Minnesota, to shed light on the broader economic implications of these tariffs.
“The primary aim of these tariffs is to raise the price of foreign steel relative to domestically produced steel,” Tyler explains. “In the best-case scenario, this could help revitalize the U.S. steel industry. However, the real challenge lies in how consumers – especially architects and builders – respond to higher prices or even the mere anticipation of them. If we simply see a reduction in steel use across construction projects, the intended boost to domestic steel production may not materialize.”
Tyler continues, “Tariffs are just one of many challenges facing the construction industry right now. Interest rates remain high, with little expectation for a meaningful decrease in the near term, and there is also uncertainty about rising labor costs.” These factors collectively create a challenging environment for architects, specifiers, builders and developers.
Proactive Measures for Architects & Specifiers
Brent emphasizes the importance of being proactive when addressing the potential impacts of tariffs. “It’s crucial for architects and specifiers to communicate the potential financial impacts of tariffs to their clients early on,” he says. “This means not only presenting the cost of materials but also suggesting alternative options or bidding alternates that can help manage those costs.”
When considering alternative materials, Brent advises that specifiers should take into account not only cost but also the availability of materials. “Heavy timber may see a resurgence, but those raw materials are also subject to tariffs. Additionally, the production facilities for these materials may not be able to quickly meet an increased demand,” he explains. “The solutions will vary depending on the region, season, and project timing.”
The Broader Impact on the A/E/C Industry
According to Brent, the tariffs on steel and aluminum are part of a larger trend that will likely slow down the construction industry. “Tariffs are just one factor contributing to this slowdown. We’re also facing rising material costs, labor costs of a shrinking workforce, and high interest rates that show no signs of falling any time soon—a perfect storm that could lead to delayed projects and increased costs,” he notes.
The Pricing Dilemma: Steel vs. Aluminum
Brent believes that the rising prices of aluminum components could have a devastating effect on the U.S. construction industry. Nearly 50% of all aluminum used in construction is imported, compared to just 25% for steel. Additionally, aluminum is significantly more expensive by weight than steel, which amplifies the impact of any price increase.
In 2018, aluminum tariffs were set at 10%, while steel tariffs were set at 25%. This disparity reflects the recognition of aluminum’s greater role in construction and the potential consequences of price and availability changes. Given aluminum's critical role in many construction applications, tariffs on aluminum are likely to have the most profound impact on the industry.
Data indicates that half of all aluminum imports are used in U.S. construction projects. Brent adds, “At 25%, the aluminum tariffs enacted this week are 150% of those briefly enacted in 2018. If aluminum tariffs increase to 50%, as some experts predict, the impact is truly unknown and frankly scary. These tariff rates are untested, and there are no ready alternatives or systems to replace aluminum. Our reliance on imported aluminum is greater than that on steel, making this a particularly pressing issue for the construction industry.”
Key Takeaways for the Metal Construction & Design Industry
The advantages of designing and building with metal remain unchanged, but the economics are evolving rapidly and unpredictably. Manufacturers and installers of metal materials can make a difference in preserving some of the economic benefits or mitigating concerns around using metal by:
- Providing upfront pricing for designers based on available materials that are less affected by tariffs or price fluctuations.
- Implement price control measures beyond raw material pricing, such as stocking fewer components, profiles or colors to help lower manufacturing and/or inventory costs.
It is essential for the metal construction industry to address the unknowns surrounding material costs. While this may seem daunting in today’s climate, it is crucial to offer solutions that mitigate cost unpredictability. Nearly all building material will face price increases, and designers will look for materials that avoid unexpected budget overruns.
“The metal construction industry must unapologetically advocate for its value proposition, emphasizing recyclability, longevity and ease of maintenance,” concluded Brent. “Additionally, the non-combustibility of metal is now more important than ever, making it a safer, more resilient choice for building design by reducing fire risk and enhancing overall structural resilience.
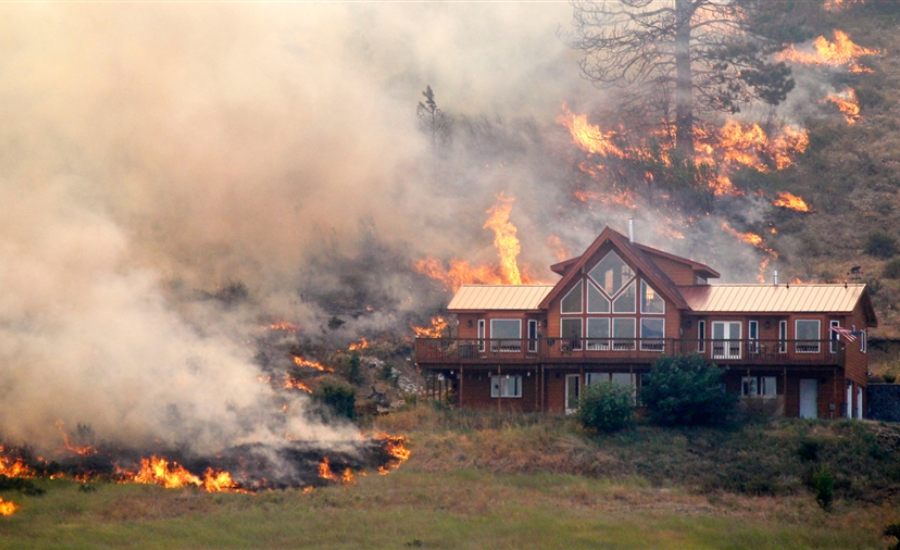
The industry will simply not have the same economic position in material selection, but with tariffs affecting many materials, the message of long-term value will likely outweigh concerns over short-term price fluctuations.”
Brent Schipper is a long-time advisor to METALCON, the world’s premier event for the metal construction industry, which features the Design District— a dedicated program for architects, designers, engineers and specifiers. He is Founding Principal of ASK Studio, an award-winning, Des Moines-based architectural platform offering master planning, architectural, interior and product design services for a diverse range of building, planning, art and cultural engagement projects.
Looking for a reprint of this article?
From high-res PDFs to custom plaques, order your copy today!