Importance of Surface Preparation in Long-Term Performance of Coatings and Sealants Reviewed at FGIA Annual Conference
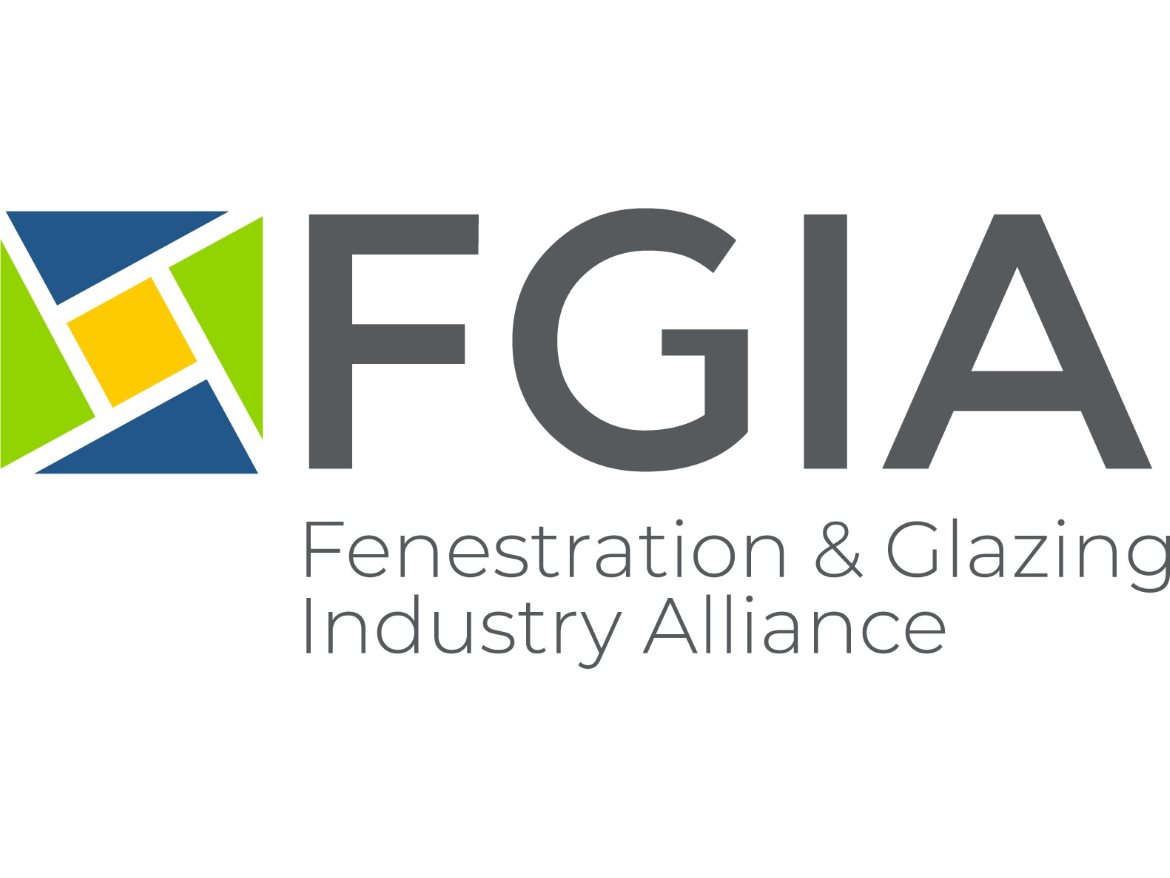
During the 2024 Fenestration and Glazing Industry Alliance (FGIA) Annual Conference, Technical Training Specialist, Aaron Blom, presented a session called “The Importance of Surface Preparation in Long-Term Performance of Coatings and Sealants.” In the start of what he said he hoped might become a series, Blom covered the benefits of surface preparation, steps to properly prepare, common problems that can arise when preparation is not conducted and how properly preparing a surface may skip one important step.
Blom began by acknowledging that the current guidance for surface preparation can vary between suppliers, and he hoped to see it become more consistent in the future. Pre-treatments are used in finishing, sealant or adhesives use and in the construction of IG units, he explained. But it is critical that glazing surfaces be free of moisture, dirt, grease, oil and other contaminating materials. “Cleaning the glass is one form of prep but is it going far enough in the pre-treatment process?” asked Blom.
Blom noted that, generally, edge seal failures can be traced back to poor or inadequate water proofing, insufficiently sized weep or vent holes, faulty glazing techniques or excessive edge pressure. Blom provided five basic steps for proper joint preparation and sealant application:
1. Clean (Surfaces are clean, dry, dust and frost free.)
2. Prime (Primer is applied to clean surface.)
3. Pack (Backer rod or bond breaker is used.)
4. Shoot (Sealant bead is pushed into joint cavity.)
5. Tool (This technique is used to strike flush joint and ensure proper sealant configuration and full contact with joint walls.)
Blom then addressed the differences between in-plant preparation and field installation preparation. “Why would field installation be any different? There are the same contaminants, plus some new ones. Surface prep is tricky because, sometimes you see it, sometimes you don't. Contaminants you don't see can cause the same problems as ones you do,” Blom said.
Blom cited the benefits of a properly prepared surface in a finishing line, such as better adhesion, a smooth and even finish as well as saved time and money. “Surface prep saves you money on callbacks on the back end,” he said. “Of course, the last benefit is long term performance.”
Blom also advised participants to avoid aggressive solvents, which can ruin finishes. “The surface must be ready on a molecular level to accept the finish,” he said.
Surface quality can be difficult to tell, Blom said. “You may need some help with measuring that,” said Blom. “You can't control the condition of the rough opening, especially in a replacement situation. A lot of factors go into surface energy, which is a measurement of readiness to interact. But if you see something that shouldn't be there, get rid of it. Take the time to do it right and deal with it.”
Finally, Blom shared that the sometimes-missed step he referenced is not having a good quality control or quality system. “Without tracking your data and your prep, you'll just keep making the same mistakes over and over,” said Blom.
Blom concluded by asking participants to let FGIA know what the Association can do to raise awareness about the importance of surface preparation.
For more information about FGIA and its activities, visit FGIAonline.org.
Looking for a reprint of this article?
From high-res PDFs to custom plaques, order your copy today!