Helping Builders Build Better with Adhesives
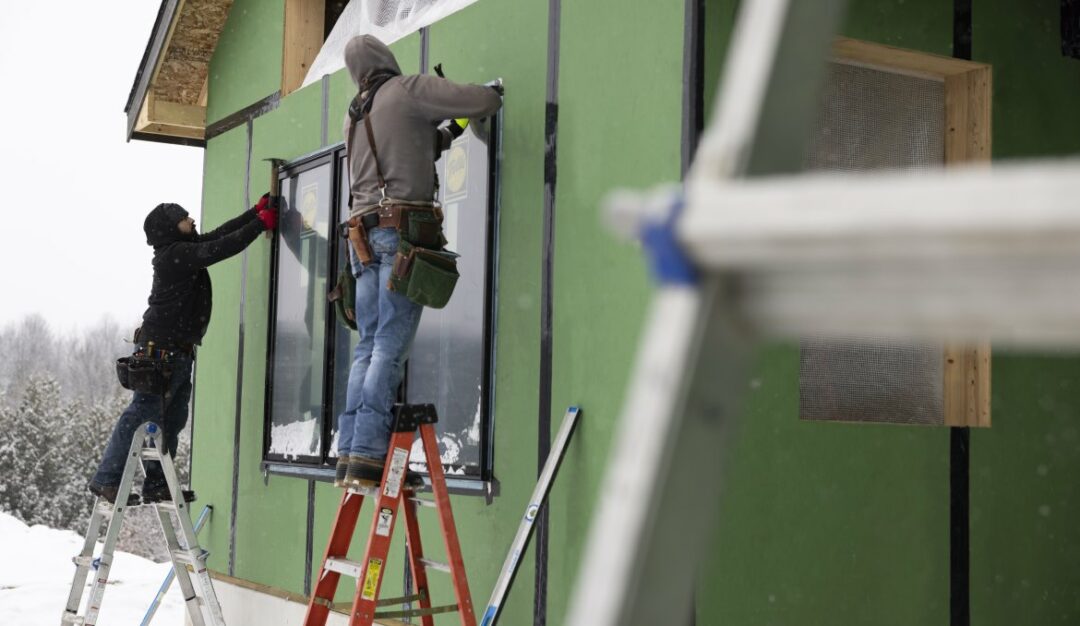
All images courtesy of Shurtape
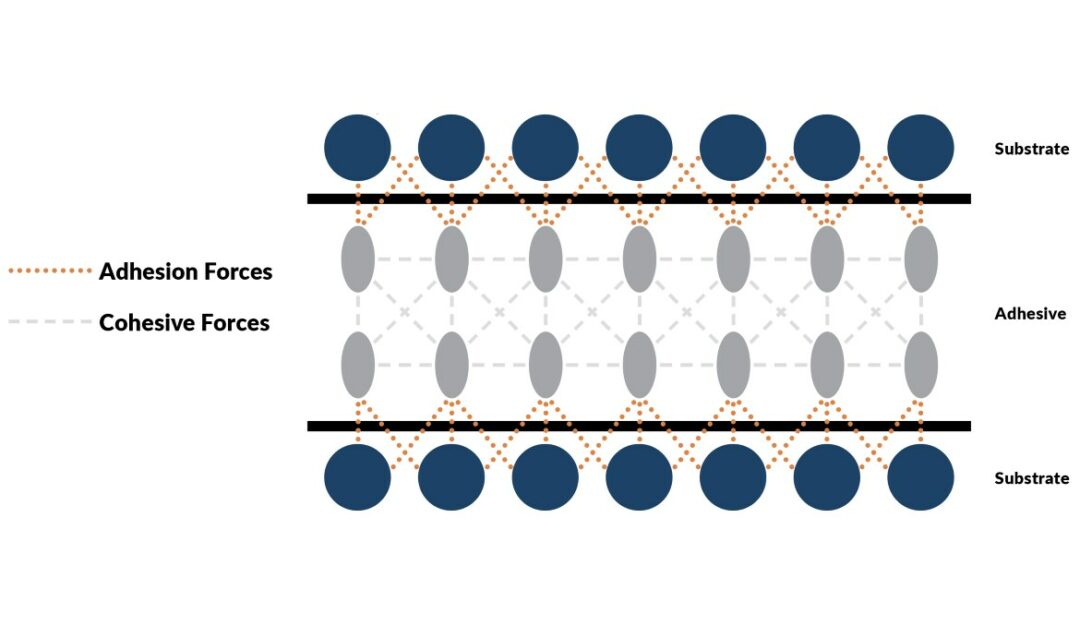


When builders approach the building envelope, it is critical they work with products that create the utmost in energy efficiency and long-term durability. But there’s more to the story than how the building envelope or enclosure performs.
Developers and contractors need to consider everything from their costs to the quality of work that building envelope products help them produce. Their bottom line, and even their reputation, rely on products that install consistently and offer long-term structural durability for their clients and customers over the long haul.
Adhesives are a key part of the equation because they directly impact the durability, compatibility and lifespan of many building envelope components. While various adhesives are available from an array of specialty manufacturers, the different technologies involved in their formulation do not perform in the same manner or to the same standards. Not all adhesives provide the balance of beneficial properties that make them capable of performing at the highest level during and after construction.
Adhesive Types & Builder Considerations
There are three main types of adhesives for building envelope applications: rubberized asphalt, synthetic rubbers and UV-cured acrylic. Each type has its place in the market. In purchasing considerations, when manufacturers who produce roof underlayment, flashing tapes and other building envelope products opt for inferior adhesives from manufacturing partners — because of cost or availability — it can create significant problems downstream for commercial and residential builders.
Builders must consider several key factors in the performance of the products they choose for the building envelope — which means it’s in the best interest of the manufacturer to create products that not only enhance performance after the building phases are complete, but also create efficiencies, improve budgets and create healthier, greener jobsites during construction.
Improving Efficiencies & Profit Margins
Among adhesive types, UV-cured acrylic adhesives represent the top tier technology for building envelope products. These adhesives are resin based and comprised of acrylic or methyl acrylic polymers. Among their attributes, UV-cured acrylic adhesives are:
- Available in liquid formulations (with water or solvents)
- Offered in formulations with 100% solids and no solvents
- Cured with UV or electron beam (EB) radiation energy
UV-cured acrylic adhesives excel in their superior aging characteristics, offering long-term durability that results from crosslinking that occurs during the curing process. The crosslinking forms polymer chains that are incredibly strong, which helps dissipate UV energy and enables the adhesive to resist chemicals and oxidation. With long-term durability comes peace of mind and reduced risks of costly callbacks to the job for building envelope failure, ultimately creating business efficiencies and improving profitability for builders.
Another key benefit of UV-cured acrylic adhesives is their broad operating temperature range. These formulations can effectively and consistently adhere from 0 F (-18 C) to over 240 F (115 C). As a result, the building season can be extended much longer into the colder months and, conversely, issues do not arise from extended exposure to high temperatures or direct sunlight during warmer months.
A broader temperature range is not only beneficial to builders by extending the building season, but it also contributes to the durability of the building enclosure by ensuring long-term integrity of seals between building components. The temperature performance range is vital to the sustainability of the building enclosure, particularly in extreme climates.
Lastly, UV-cured acrylic adhesives allow for primerless adhesion, which translates to faster installations with fewer steps in the process. Many butyl rubbers require primers to be used with certain construction surface materials, especially in cooler temperatures. Primers delay projects due to the time needed for application and drying that varies depending on weather conditions. These both slow the building envelope assembly process and introduce the potential for application error.
Enhancing Building Envelope Performance
Advanced UV-cured acrylic adhesives are highly versatile, perform in a broader temperature range, create stronger bonds and contain low or no volatile organic compounds (VOCs) that off-gas and dry out the product over time.
UV-cured acrylic adhesives also have a high affinity for adhering to a variety of surfaces, including those with low surface energy due to their highly polar functional monomers. Products using this adhesive technology are repositionable for a short time allowing installers the ability to align components. Full adhesion can take 24 to 72 hours for some low surface energy materials. The unique flow properties of the adhesive enable it to flow into surface inconsistencies, producing a permanent, lasting bond.
The highly-crosslinked polymer chains in UV-cured acrylic adhesives also create extremely strong molecular bonds that are stable against UV light. As a result, they do not break down like rubberized asphalt and synthetic rubbers in prolonged exposure to sunlight. They are also highly resistant to extreme temperatures, chemicals and oxidation, which means they are extremely durable and can withstand seasonal temperature fluctuations without sacrificing performance.
Creating Safer, Greener Jobsites
In addition to drying out adhesives from off-gassing, VOCs can cause a wide array of negative health effects, including eye, nose and throat irritation; headaches; loss of coordination; and nausea. Prolonged exposure can cause damage to the liver, kidneys and central nervous system and even cause cancer. Plus, VOCs are well known to cause harmful air pollution — both indoors and outdoors — as well as smog.
VOCs are released into the air as gasses from certain solids or liquids. They include a variety of chemicals and their concentration in our air that is consistently higher indoors (up to 10x higher) than outdoors. They are emitted by a myriad of products, including building materials and adhesives. It is no wonder, then, that low- or no-VOC products are preferred on the jobsite — it makes working with these products safer in the short and long term.
The volatile organic compounds contained in rubberized asphalt, for example, lead to issues with product/component durability and compatibility, as well as negative environmental impact. As the VOCs off-gas and the adhesives dry out over time, the adhesives lose their pliability and flexibility, which can result in debonding and potential leaks as the building components shift throughout their lifespan due to climatic changes.
The VOCs and solvents in rubberized asphalt can react negatively with other materials used in the structure’s construction. Materials such as caulking, sealants and vinyl window flanges often contain solvents and other chemicals that are incompatible with rubberized asphalt. When the materials come into contact with each other, they degrade. This can cause not only reduced adhesive effectiveness but an unsightly and even damaging mess that could lead to litigation against contractors and suppliers.
Synthetic rubber and UV-cured acrylic adhesives both include a material makeup that is free of solvents or VOCs; however, UV-cured acrylics offer the added benefit of high performance in demanding climates.
Partnering Wisely
It is critically important for building envelope product manufacturers to make the best possible choice in adhesives partners. The integrity of their products directly impacts structural durability and energy efficiency, as well as the health and welfare of both installers and future building occupants.
UV-cured acrylic adhesives offer next-level performance throughout the building envelope and should be at the top of the list of considerations when choosing an adhesives partner. The performance, health and sustainability benefits of UV-cured acrylic adhesives combine for more successful building envelope projects that benefit contractors, installers and builders — as well as the people who live, work, learn and play in the structures they build.
To learn more about adhesive products for the building envelope, visit shurtapespecialty.com/Building-Envelope
Looking for a reprint of this article?
From high-res PDFs to custom plaques, order your copy today!