OSHA Voluntary Protection Program Serves as Valuable Safety Resource
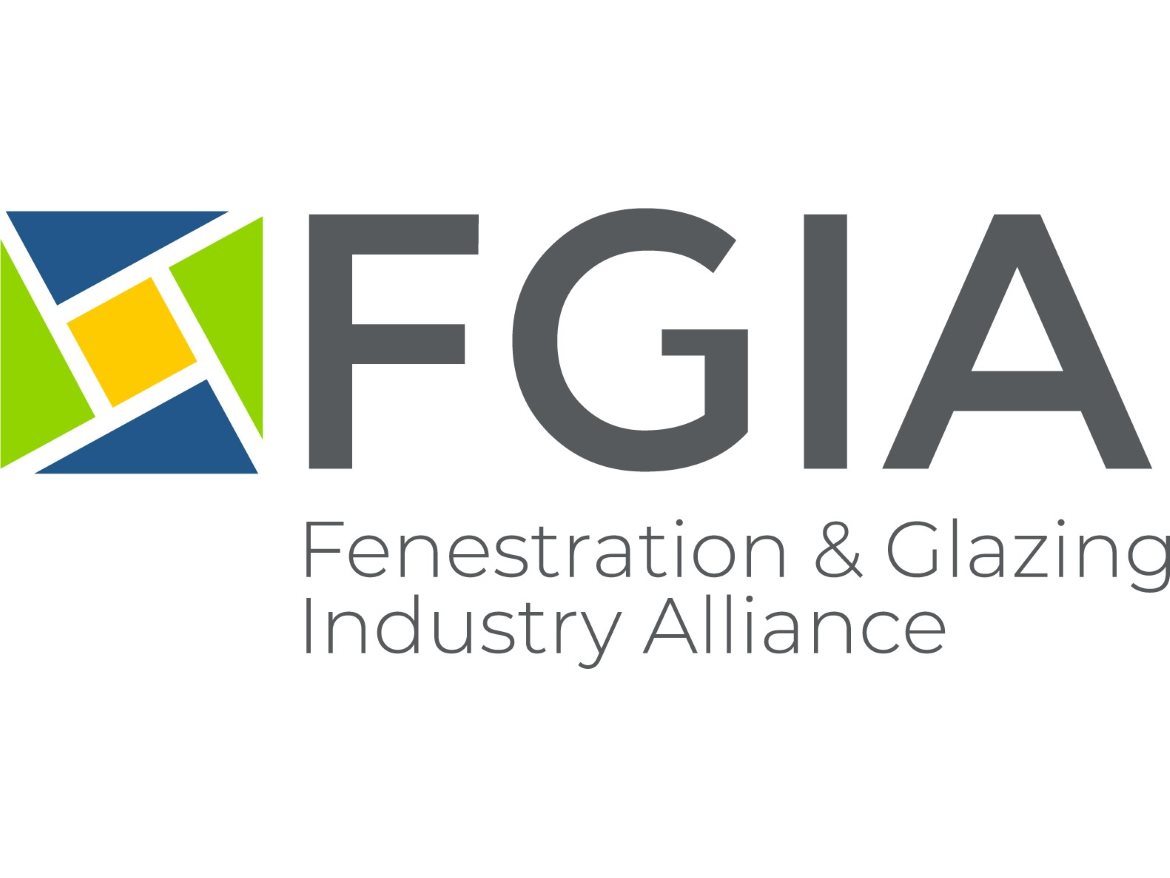
Participants at the Fenestration and Glazing Industry Alliance (FGIA) 2021 Virtual Summer Conference learned more about a voluntary safety program focused on excellence from one of its administrators as well as an FGIA member company participant. Brad Baptiste, regional Voluntary Protection Program (VPP) manager for OSHA Region VIII, and Rob Grommesh, insulating glass (IG) technical service manager for Cardinal Glass Industries, shared how manufacturers can succeed in safety through the OSHA VPP, which seeks to help manufacturing sites reach zero incidents and injuries.
According to Grommesh, Cardinal made the decision several years ago to seek OSHA VPP certification for all its facilities and is currently halfway toward that goal. "Cardinal prides itself on striving to perform, look and be the best in the industry across functions," said Grommesh. He noted that Cardinal had a strong safety program but didn't realize what "world class" was until starting the process of becoming VPP certified.
"I commend participants on being committed to safety and health," said Baptiste. "VPP is a partnership between you, your employees and OSHA. It benefits workplaces in several ways, including decreased turnover and absenteeism, increased productivity, exemption from programmed OSHA inspections and community recognition. Plus, being involved in VPP gives you a competitive edge when it comes to getting contracts."
It also benefits workers, explained Baptiste, who can be more confident they will go home safely at the end of the day. "In VPP, employees are actively engaged in safety and health," said Baptiste. "They become deputized to protect themselves and their coworkers, taking an active role on the job."
Baptiste shared some 2018 data about the program, at which time there were 1,120 VPP sites across 280 different industries, representing more than 400,000 employees. Around 40 percent of those sites had zero recordable injuries in 2018, saving an estimated $440 million in injury costs. "This is a non-enforcement program and there is no fee to join," he said. "You submit an application and if it is accepted, we come in for an on-site evaluation. No citations, no penalties."
Once a site's application is accepted, there is an evaluation process. During this, a team of OSHA personnel visit the site for four or five days. The evaluation consists of an opening conference, document review, a walkthrough of the worksite, employee and management interviews and a closing conference. Then, a draft report and recommendations for one of three programs are provided.
"Typically, most organizations that complete [the evaluation process] do receive VPP at some level," said Baptiste. "But every journey begins with the single smallest step."
Baptiste noted that a common question from companies is, what happens if hazards are found during the evaluation? "We point those out at sites and ask you to fix them in 90 days," he said. Again, no citations are issued, nor are penalties incurred, Baptiste said.
Baptiste said the keys to VPP success are management commitment and active, constructive employee involvement. Continual improvement leads to long-term sustained levels of high performance. "'Cultural excellence' goes well beyond safety," he said. "You will see quality and profitability increase as well, and long-term success."
Grommesh agreed, saying VPP certification for half of Cardinal's locations has been a lifestyle change. "They are much more safety aware. They work hard to maintain certification." At his own site, Grommesh said they have gone more than two years with zero incidents. "It really is an amazing thing to go into these plants and hear people talk about their pride in achieving this distinction," he said.
Visit osha.gov/vpp to learn more.
For more information about FGIA and its activities, visit FGIAonline.org.
Looking for a reprint of this article?
From high-res PDFs to custom plaques, order your copy today!