Atlas Brings Sustainability to NoHo West Mixed-Use Community & Redevelopment Center
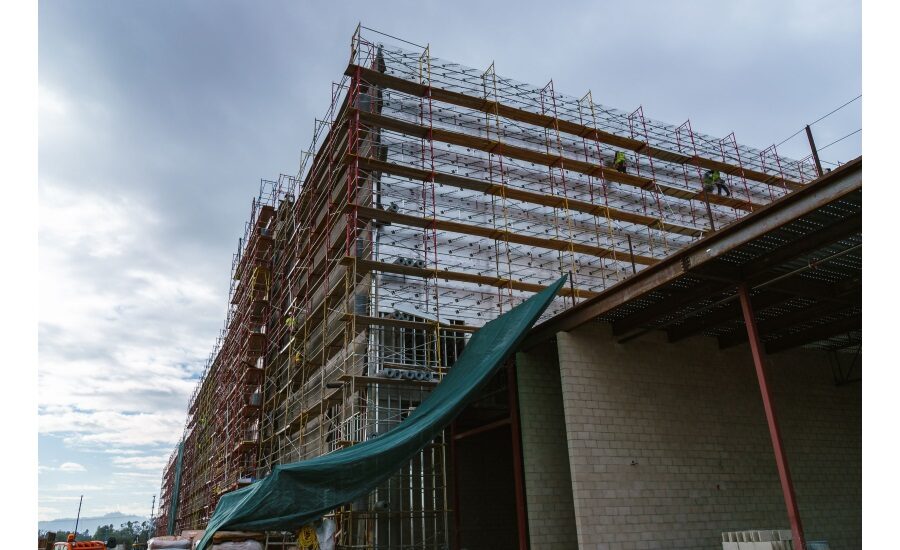
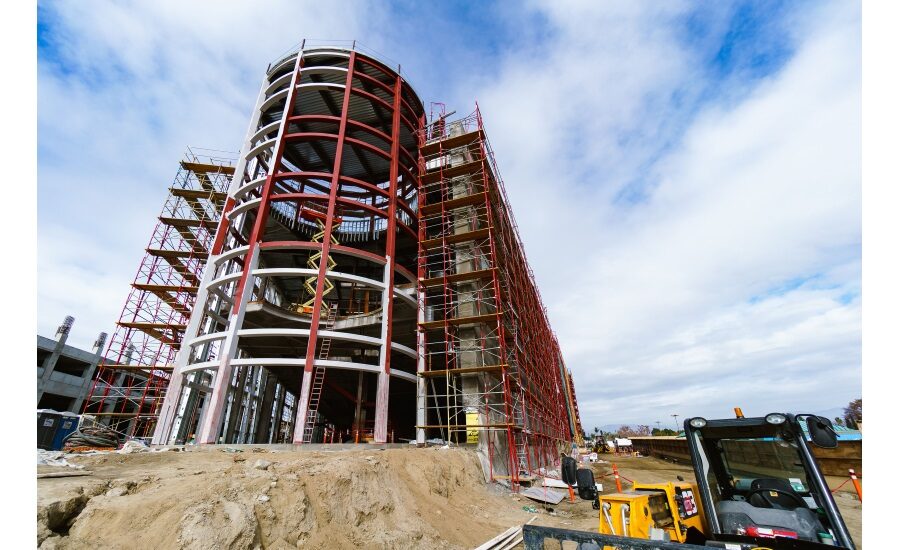
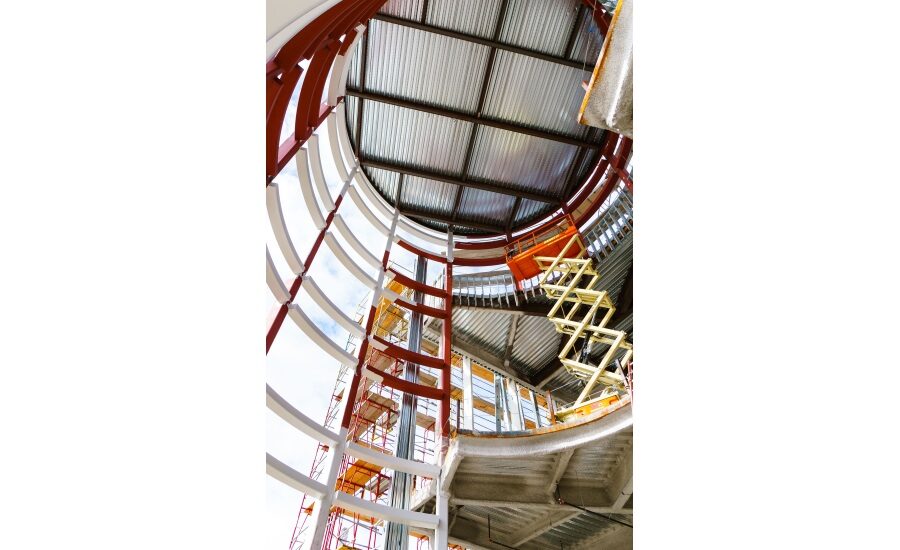



Project Challenge
Built in 1955, Laurel Plaza in North Hollywood, California, has had quite a history – and is now entering the next phase of its story. The building transitioned from its original May Co. store to a bustling shopping center with Macy’s as its anchor before suffering significant earthquake damage a few years ago. The forgotten and dilapidated shopping center is now well on its way to revitalization thanks to new developers with a vision.
The former Laurel Plaza will soon become NoHo West, a mixed-use community complete with creative office space, apartments and retail. The project will include a variety of environmentally friendly features, like electric car charging stations, bicycle parking and a solar energy canopy above the parking garage. Due to the progressive and forward-thinking nature of this project, it was decided to design and build the new development to comply with impending 2020 California code that will require continuous insulation in all new constructions. Additionally, new design needs and costs required valuing engineering to cut down on budget and construction schedule.
Approach
The building owner, Merlone Geier Partners, and Los Angeles-based STIR Architects called for continuous insulation as the backbone for new exterior wall systems that would become the standard of 21st century construction. The building’s original design called for continuous insulation to be applied with the water resistive barrier (WRB) membrane adhered to the face of the continuous insulation. After additional budget and scheduling needs were considered, the design and construction team needed to find ways not only to reduce the construction cost and timeline, but also to reduce the project’s overall carbon footprint. Tim O’Conner, with Superior Wall Systems (SWS), the subcontractor responsible for exterior wall systems on this project, worked closely with insulation manufacturer Atlas Roofing Corporation to alter the wall assembly for better performance and reduced labor and cost. SWS decided to use the exterior wall insulation as the WRB as well. This new assembly allowed the removal of the adhered sheet WRB in favor of taping the joints of Atlas EnergyShield Pro. EnergyShield Pro is a foil faced continuous insulation and, when an approved tape is properly adhered, can fulfill the needs of a WRB. Additionally, EnergyShield Pro is a versatile insulation and is compatible with the multiple types of cladding used on this project.
SWS and Atlas were able to provide a solution to the architect and building owner that not only met these specific design needs, but also ensures long-term energy efficiency and reduced the project’s carbon footprint and construction schedule by eliminating construction materials. With the pending 2020 California code changes on the horizon requiring exterior wall systems to include continuous insulation, the team had to choose the right materials for regulatory compliance with the design flexibility needed to support the vision of the project. As an expert in polyiso manufacturing with more than 30 years of experience improving building envelope performance, Atlas EnergyShield Pro became the ideal choice.
Tim O’Connor, SWS’ Pre-Con Director and Chief Estimator, worked closely with the Atlas team to find a system that would meet all the design and code requirements.
A third-party testing company performed an inspection to validate the use of EnergyShield Pro as the WRB in lieu of a peel and stick membrane on the project. Results of the testing determined the use of EnergyShield Pro as the WRB was acceptable and met all necessary requirements.
Impact
Because the team chose a solution that could serve as both continuous insulation and WRB, they were able to decrease material and labor costs while shortening the construction timeline. This multifunctional solution additionally reduced the environmental impact caused by excess construction materials and waste. Thanks to the high R-Value and energy efficiency of Atlas EnergyShield Pro, the exterior wall system will have fewer thermal breaks thereby saving on long-term energy costs. With less pressure placed on the building’s HVAC system, Atlas EnergyShield Pro, which is GREENGUARD Gold certified, also will reduce the building’s overall carbon footprint due to reduced heating and cooling needs. All visitors to the new NoHo West development will now enjoy a comfortable place to live, work and play in a revitalized – and green – neighborhood hub.
Looking for a reprint of this article?
From high-res PDFs to custom plaques, order your copy today!