Resilient Engineering Against Natural Disasters
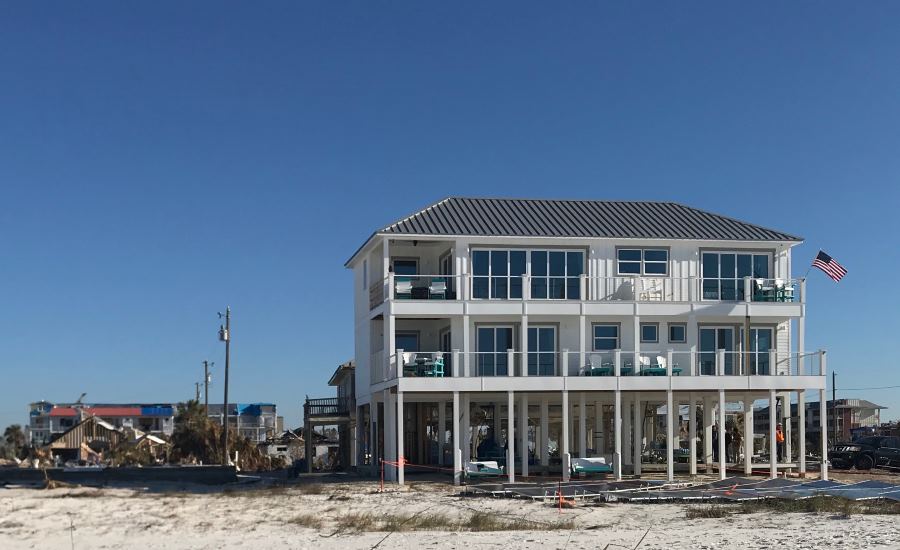
Wiped out. That’s how the Federal Emergency Management Agency described Mexico Beach, the Florida seaside resort town where Hurricane Michael made landfall on October 10. Packing sustained winds of 155 mph, Michael pummeled Mexico Beach with a 9-foot storm surge, leveling homes and businesses in its path. By the time the storm finally cleared, it had tragically claimed 60 lives and some $11.28 billion in damages.
Miraculously, one beachfront home emerged from the storm practically unscathed, and in the weeks following, aerial photos of the house still standing amidst the destruction levied by the hurricane went viral on the internet. Websites like Popular Science detailed the home’s resilient engineering, and Coastal Living called the house an overnight symbol of storm strong construction.
Built in 2017 by radiologist Lebron Lackey and his uncle Russell King, the vacation home known as the Sand Palace was constructed to withstand winds up to 250 mph, and features poured concrete walls, fiber-cement siding, and an aluminum roof attached to the house with hurricane ties.
“We wanted to build something right, something that would last for generations,” says Lackey of the engineering behind the building. “Resilient construction ultimately comes down to your comfort level. You can build to code or you can build beyond code, and once you build beyond code, you just need to decide how comfortable you are that you’ve built things strong enough and don’t need to engineer to the next level.”
Indeed, next-level engineering defines the Sand Palace from pilings to pitch, and begins 28 feet beneath the mean water level, where support pilings driven into the sand reach bedrock. Although code required only 30-foot pilings, Lackey and King opted for 40-footers, providing a bomber foundation that also allowed for 12 feet of storm surge flow between the ground and the first floor of the home. Rebar extended through the pilings and girder into insulated concrete form (ICF) walls 12 inches wide, which featured an additional plastic cross lattice to support rebar, and the entire home boasted steel-reinforced corners. “So from 28 feet below the ground to the roof, we are literally built as a single mass of concrete and steel,” Lackey says.
Due north up Interstate 75 from Mexico Beach, researchers at the Insurance Institute for Business and Home Safety (IBHS) are studying ways to improve construction and incorporate resiliency into building codes. Not surprisingly, side-by-side testing of structures built below code, built to code, and built beyond code at the IBHS Research Center show drastic performance differences when subjected to simulated natural disasters including hurricanes, tornadoes, and wildfires. Not so intuitive, however, is how well homes perform when they are built to code or slightly above code standards.
“The IBHS facility is large enough to build two-story houses side by side on the testing floor and have hurricane-force winds blow on the houses with this incredible wall of high-powered fans,” says professional engineer Sam Hensen, who is the vice president of connectors and lateral systems for Pleasanton, Calif.–based Simpson Strong-Tie.
According to Hensen, structural resilience across the nation’s housing stock could be vastly improved if stakeholders from homeowners to contractors to inspectors embraced the simple discipline to build to code and inspect to code before certifications of occupancy are awarded. “Part of what the IBHS tests show is that resiliency isn’t just about new innovations, it is about building to code or just above code and then inspecting buildings to make sure construction is done properly,” he says. “Are we working on innovations for more intuitive, easier-to-install products, and construction efficiency? Of course, we’re constantly trying to improve, but if people just follow code, or maybe build just a little better than the code, structures are going to fare much better in a wind event.”
In particular, Hensen recommends all builders adopt continuous load path engineering to ensure that loads are adequately transferred from roof to foundation during high-wind and seismic events. Already a mainstay of Miami-Dade County building codes and the engineering standards developed by the IBHS FORTIFIED Home program, continuous load path engineering uses a system of wood, metal connectors, fasteners and shear walls to tie the structural frame of the house together, holding the home in one piece when ground forces or high winds might otherwise pull a structure apart.
“If we look at Hurricane Michael, homes following the FORTIFIED program fared really well in what became one of the most powerful hurricanes to ever hit the contiguous United States,” Hensen says. “And the cost to build just above the local wind requirements was less than 10 percent. From a connector standpoint, just tying the roof to the walls and the walls to the foundation was only $500 more to properly reinforce the houses.”
While the use of poured concrete at the Sand Palace mitigated the need for continuous load path structural systems, Lackey nevertheless paid critical attention to roof engineering as he carefully evaluated code—and how to cost-effectively supersede it—while building his super home. “As you have oncoming wind, it needs to deviate around the mass of the house and as you have a downward force on a sloped roof it has to be transferred to walls that can support it,” Lackey says. “Conceptually we didn't have to worry as much about the force as it went down the wall, we just needed to make sure the roof stayed on.”
The resulting wood truss, hip roof was attached to the walls with hurricane ties to secure the roof trusses, and soffits were closed with fiber cement. Despite being subjected to incredible wind forces during the storm, the Sand Palace and its roof remained intact, and a video camera attached to one corner of the home actually transmitted imagery throughout the duration of the hurricane. “You could see the movement on the eave, and it was unbelievable, the force of this movement, but the video feed kept going through the entirety of the eye wall, and I knew at that point I still had my roof,” Lackey says.
According to Lackey, fortifying the Sand Palace beyond code levels was an exercise in engineering research and cost management that proved resilient construction can be achieved with minimal increases to material and labor investments.
“Pretty much from the get-go, we tried to understand why the code was written the way it was. We’re cognizant of the fact that code considers a lot of interests from politicians to the insurance industry to construction professionals to homeowners,” Lackey says. “It’s very natural that the next question to ask is how expensive it would be to go beyond code, and everything we are talking about for this building is off-the-shelf product, nothing is custom made for this house. It is within reach of anybody.”
Hensen agrees, and says the typical cost increase to achieve continuous load path in a wood-built structure is a paltry 25 cents per square-foot, an investment about which most homeowners should be better educated as they select options and upgrades. “The technology is sound, and we have been using the products for a long time in ways that show a home is more likely to withstand a seismic or high-wind event and stay intact when all parts of the house—roof, walls, floors and foundation—are connected together,” Hensen says. “And yet the perception is that homeowners are uninterested in structural upgrades, and the flooring and countertops are what’s most appealing.”
Lackey, for one, is ready to broadcast the value of resilient construction far and wide, and agrees that the building industry could take a positive step forward in that regard. The end result, he says, could be a much different post-hurricane coastline than what was seen in Mexico Beach—one where the majority of homeowners would be able to return home and wipe things clean instead of being completely wiped out. “Whether it is the Weather Channel or HGTV or the DIY Channel, the building industry needs to be more invested in creating a more educated consumer,” Lackey says. “Homeowners need to understand resilient construction is within reach, and they need to ask for it by name.”
Looking for a reprint of this article?
From high-res PDFs to custom plaques, order your copy today!