Waterproofing Codes: Joints and Penetrations
Section 1807.3.3
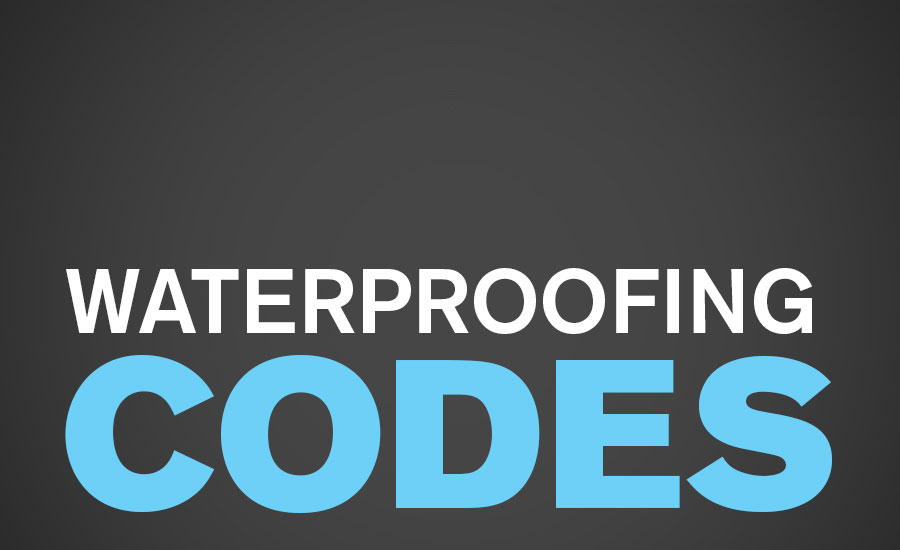
1807.3.3
JOINTS AND PENETRATIONS
Joints in walls and floors, joints between the wall and floor and penetrations of the wall and floor shall be made water-tight utilizing approved methods and materials.
CODE INTERPRETATION
This section implies that all wall and floor joints must be properly waterproofed. Waterproofing application at joints includes approved sealants. Proper sealant application is completed using proper materials and application methods.
The success of the construction sealant is based on proper selection and use of the various sealant materials for a specific application. Sealant selection should be based on the adhering substrates. General recommendations for sealant selection typical in roof applications are as follows:
Concrete-to-Concrete: Two part polyurethane
Brick to Brick: Two part polyurethane
Metal-to-Metal: Perimeter silicone sealant
Metal to Brick: Perimeter silicone sealant
Metal-to-Metal: Perimeter silicone sealant
Metal to Brick: Perimeter silicone sealant
The sealant must have the ability to move with the adjacent building substrates while maintaining a watertight barrier. In application it is generally discovered that a thin bead of sealant will accommodate more movement than a thick bead. In joints where excessive movement is expected the building sealant should be no thicker than 1/2 inch and no thinner than 1/8 inch.
At typical building joints the ratio of joint width to sealant depth should be a minimum of 2:1. At building expansion joints the designed joint should be at least twice the total anticipated joint movement. However, due to construction tolerances and material variations it is recommended that the joint design be four times the anticipated movement.
Preparation of the Joints
The joint must be thoroughly cleaned prior to any sealant application. This can be completed by removing all foreign matter and contaminants such as grease, oil, dust, water, frost, surface dirt, old sealants and protective coatings.
Porous substrates can be cleaned by grinding; blast cleaning (sand or water) saw cutting or mechanical abrading. A combination of these cleaning methods can also be utilized. All dust and loose particles from these cleaning operations must be removed by vacuum or compressed air to leave a dry, clean surface for sealant application.
Metal, glass and plastic surfaces can be cleaned with mechanical or solvent procedures. Check the manufacturers latest printed specifications for the use of detergent or soap and water treatments, they are generally not allowed as suitable cleaning methods. Solvents should be wiped off with clean, oil - and - lint - free cloths.
Masking
All areas adjacent to the building joints should be masked prior to sealant application. This is to allow for neat sealant lines. Masking the adjoining surfaces also guards against sealant contact with any incompatible surfaces. Uncured sealants can leave a film on a surface that may change the aesthetic surface characteristics of the substrate. In some cases, the only method of sealant removal may be grinding or saw cutting. Generally these surfaces can be cleaned with special cleaning solvents.
The masking should be removed immediately following the tooling of the sealant.
Sealant Application
Install all back up material or joint filler prior to sealant application. Backer rods and joint filler material must be in accordance with the manufacturers latest printed specifications. Open cell polyurethane foam or closed cell polyethylene are the recommended back up materials for most joints. Polyethylene tape may be used for joints that are too shallow for backer rod.
The sealant should be applied in a continuous operation using positive pressure to properly fill and seal the joint. Tooling should be completed in a continuous stroke immediately after the sealant application prior to the formation of the sealant skin. The sealant should be tooled with light pressure to spread the material against the back up material and the joint surfaces.
The tool should have a concave profile to keep the sealant in the joint. Contrary to popular opinion, a finger is not the proper tool for sealant application.
Looking for a reprint of this article?
From high-res PDFs to custom plaques, order your copy today!