Dryvit Launches Tech21 Initiative
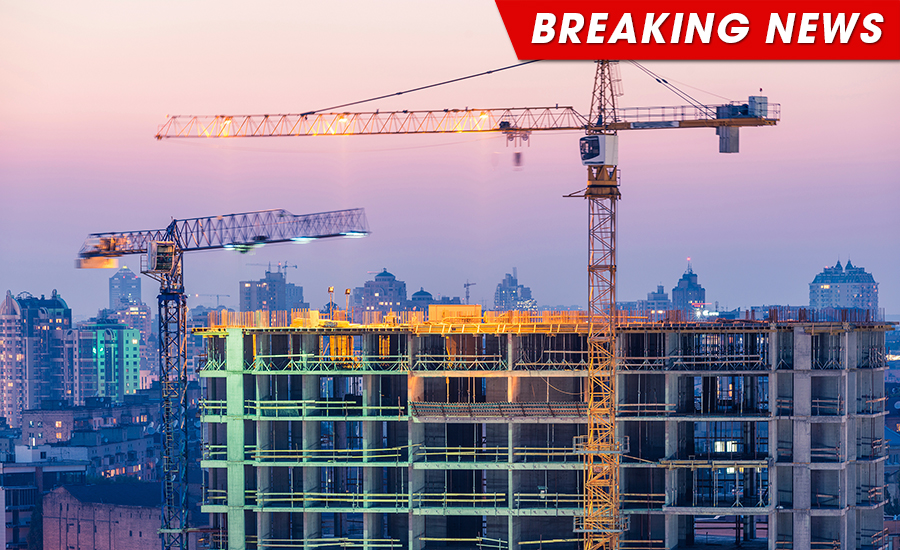
Dryvit Systems Inc. announced the launch of its Tech 21 Initiative, a new program to make it easier for building owners, general contractors and architects to use or specify prefabricated panels of Dryvit’s Outsulation systems with Dryvit’s traditional EIFS finishes or its NewBrick cladding.
The Tech 21 initiative will be led by Rick Bunting, who has been named to a newly created position as Dryvit’s National Renovation and Panelization Manager. Bunting brings more than 35 years of experience in the commercial and residential construction industry to Dryvit. He previously served as a regional sales manager for Eastern Exterior Wall Systems Inc., an industry leader in the development of prefabricated wall systems. Bunting also served as an independent consultant specializing in wall systems.
A key role for Bunting in his new position will be to help expand the growing ranks of contractors already prefabricating Dryvit panels to help ensure a readily available supply across the U.S.
“There is a growing demand from building owners, general contractors and architects for prefabricated, lightweight exterior cladding panels that meet the latest energy codes and can be manufactured offsite and brought to the job site for rapid installation,” said Mike Murphy, Dryvit’s President and CEO. “We’re excited to help meet this need with our innovative Tech 21 program that will not only increase production capacity for our prefabricated, energy efficient Outsulation panels, but also provide added resources for contractors setting up or operating prefabrication facilities. The bottom line consideration for building owners with our Tech21 initiative is the ability to save time and money.”
The use of Dryvit’s prefabricated panels helps address two major challenges in new construction or major renovations: the need to accelerate completion of a building’s exterior cladding and the shortage of skilled labor.
“Accelerated installation of a building’s exterior cladding through panelization enables a property to begin generating revenue much earlier than if traditional, field-applied construction is used,” said Dryvit’s Bunting. “The added value of overcoming labor shortages by prefabricating Outsulation panels in areas of the country where skilled labor is more plentiful is also a huge bonus.”
As part of its Tech 21 initiative, Dryvit has launched a Partner Fabricator Network that provides premium warranty coverage for prefabricated panels manufactured by participating contractors. Contractors who undergo additional training and meet other qualification standards are eligible to participate in the Partner Fabricator Network.
Another benefit of using pre-fabricated Outsulation panels is a reduction in the need for scaffolding on tall buildings, a financial savings that also carries valuable safety benefits. Dryvit’s prefabricated panels also give architects greater flexibility in incorporating more complex design elements that are more easily built in a prefabrication facility than on the job site with field applied EIFS.
“For many general contractors and building owners today who are choosing EIFS, field applied EIFS isn’t an option because they need to complete the exterior cladding on an accelerated basis,” said Rob Little of Indiana-based Little Construction, a company that has been panelizing Dryvit’s systems for decades. “The speed and safety factor of not having EIFS installers on scaffolding on the outside of a building for a longer period of time is a huge payoff. Lifting panels with a crane or a boom lift can allow you to finish a job in a few days compared to weeks upon weeks of installers working on scaffolding. That makes a huge difference not only on the number of man hours that you need but also in significantly reducing the risk of workplace injuries.”
Dryvit’s Tech 21 initiative comes at a time when many of the nation’s largest building owners are relying more and more on the use of prefabricated building components to accelerate construction and ensure high quality building components by relying on a select group of proven contractors that can build components in controlled conditions.
In addition to prefabricated exterior cladding panels, other major building components being prefabricated offsite include load bearing steel stud partitions that eliminate the need for structural steel and allow floors to be installed as a single, modular unit. Prefabricated bathrooms for hospitals and school campuses are also seeing major growth.
The rapid growth in the use of prefabricated building components is being led by some of the most recognized names in the commercial real estate industry. Last year, Marriott Hotels announced plans to incorporate a modular construction option for new hotel construction. Currently, Wynn Casinos is building a new casino in Everett, Massachusetts that is being built with 300,000 square feet of prefabricated Dryvit Outsulation panels.
Contractors, architects and building owners interested in learning more about Dryvit’s Tech 21 initiative, including the Tech21 Partner Fabricator Network, can visit www.Dryvit.com/tech21 for more info.
Looking for a reprint of this article?
From high-res PDFs to custom plaques, order your copy today!