Campus Building Achieves LEED Silver
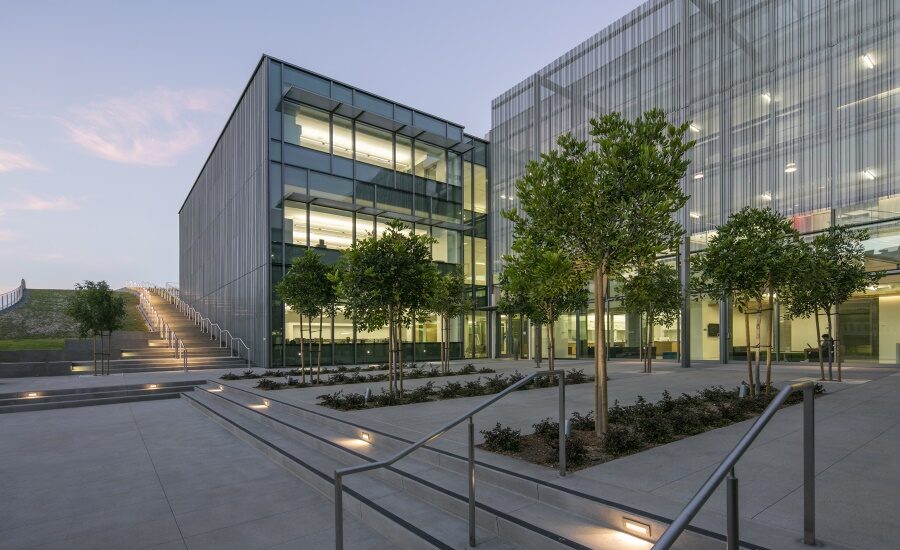
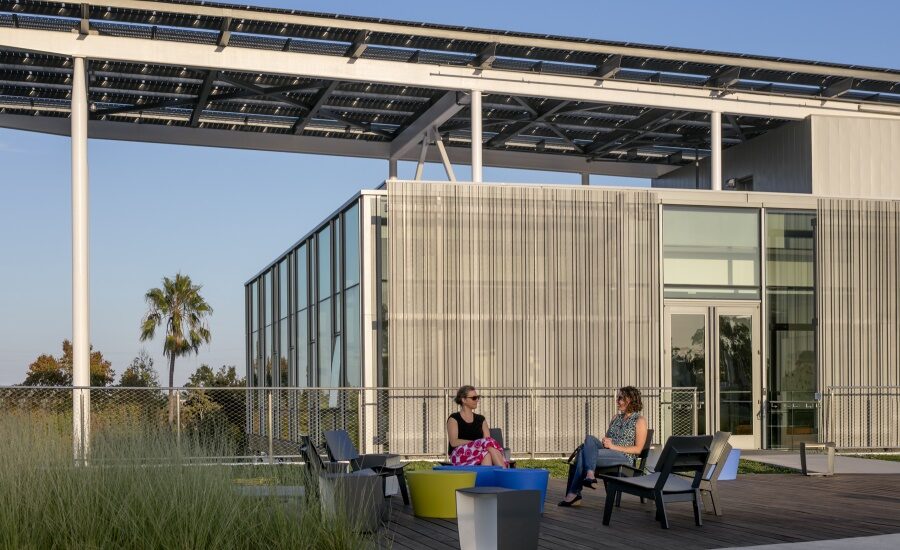
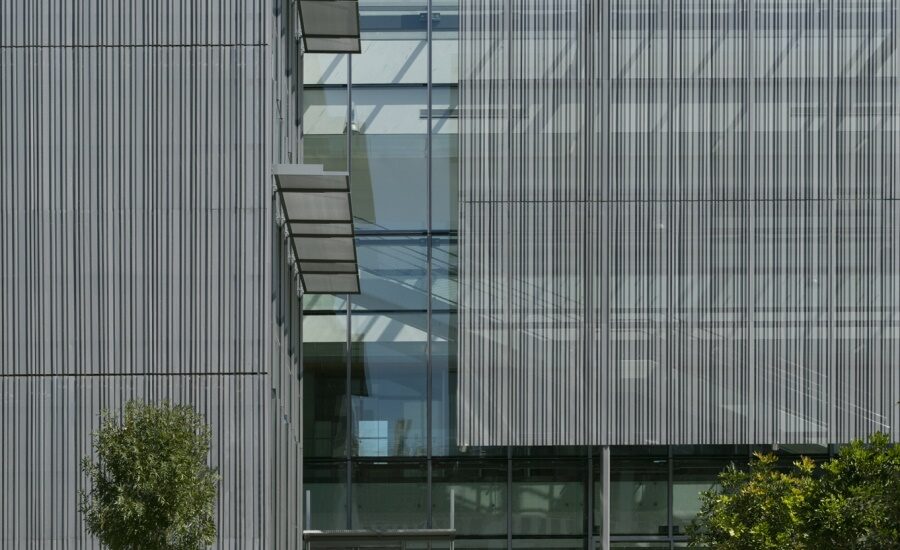



As the first building designed under Loyola Marymount University’s (LMU) Campus Master Plan, the Life Sciences Building sets the pace for modern, sustainable design at the university. Located on bluffs overlooking the Pacific Ocean, LMU is the largest Jesuit Catholic university for undergraduates on the West Coast.
The project integrated three primary objectives—“interdisciplinary collaboration,” “science on display,” and “sustainability,” according to CO Architects, Los Angeles. The CO Architects team designed a building that not only acts as a daily teaching tool but establishes a new architectural standard for the campus.
The 100,000-square-foot, LEED Silver facility includes 35 research and teaching labs, 9,000 square-feet of faculty research space, nine student study areas and a 273-seat auditorium.
“Our primary design objectives included the integration of two departments—chemistry and biology—while providing maximum transparency to the building so that everyone could see what’s going on in the two departments,” said James Simeo, CO Architects principal. “And doing so with an environmentally-friendly and highly-executed sustainable design,” he added.
Nearly 10,000-square-feet of prePATINA blue-grey RHEINZINK helped accomplish the sustainability and design objectives. The RHEINZINK was fabricated as a perforated screen and attached to the western side of the building.
“We were constrained by the site to have the building oriented in a north/south configuration which meant lots of glass that was going to face east and west. We had to control the western sun,” Simeo said. “The area where the RHEINZINK perforated screen is located is the main staircase entry on the west side of the building. It’s a place with lots of glass for transparency where students congregate and people go to and from various floors.”
Instead of attaching the screen directly to the façade, the design team created a significant space between the screen and the curtainwall. “We kept it somewhat away from the building so that it functioned more like a scrim,” according to Simeo. “It became its own architectural element and provides a lovely veil in front of the glass that people can see through and yet it significantly helps control the heat gain.”
The design team selected zinc for the screen at an early stage of the design process although the dean had to be convinced. “Initially, he was a little concerned about the screen itself and the grey color,” Simeo said. “But we convinced him that the screen would be aesthetically pleasing and highly functional as well. And importantly, that zinc was the right material. We did several mockups showing the perforated RHEINZINK screen and he quickly warmed to the idea that using a natural material could serve as a learning tool for the students. To be able to see a natural metal outside the windows of the chemistry teaching labs was an important factor.”
The firm designs with zinc whenever it can, according to Simeo. “We love zinc because it’s a natural metal. And it weathers beautifully in a site like this which is only a mile away from the coast with lots of salt in the air. We didn’t want something that would show rust spots or have to be repainted in 20 years,” Simeo added. “The zinc was the absolute right material which is why we fought so hard for it. We like RHEINZINK a lot,” he said. “It’s a good company. The product is great. We specify it whenever we can.”
Fabrication and installation of the RHEINZINK perforated screen was accomplished by CMF Inc., Los Angeles.
The RHEINZINK distributor on the project was Old Country Millwork (OCM) Inc., Los Angeles.
For more information on RHEINZINK, call 781-729-0812 or visit www.rheinzink.us.
Looking for a reprint of this article?
From high-res PDFs to custom plaques, order your copy today!