Waterproof Roofing Underlayment on Steep-Slope Roofs
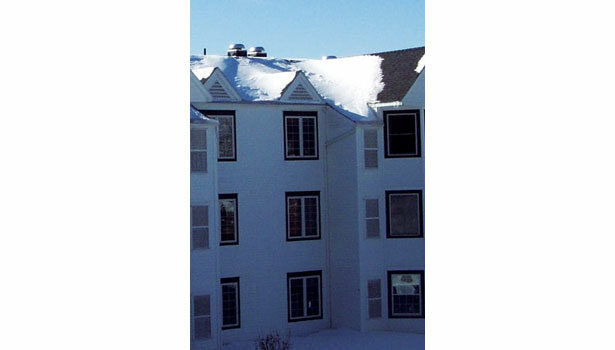
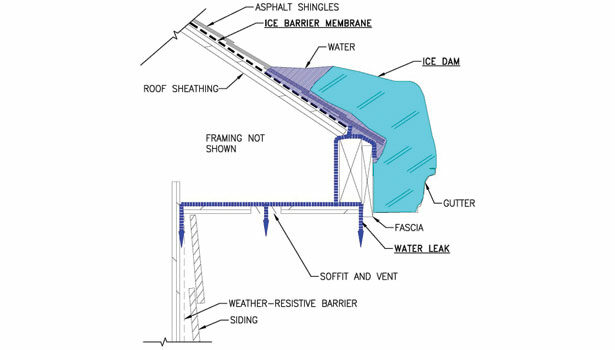
FIGURE 1: This detail shows how water can leak through the sheathing/fascia joint and/or lap joints in the eave edge metal into the soffit and/or building wall.
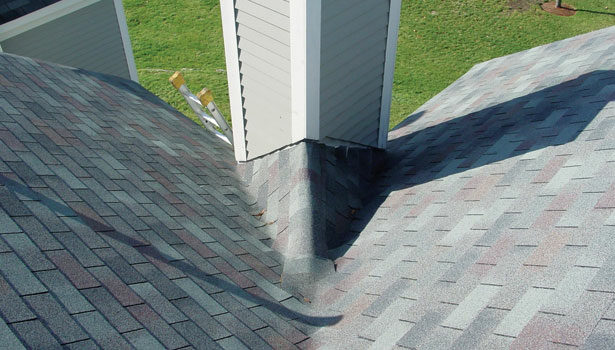
Photo 2: Roofs with obstructed valleys or pinch points create a greater risk of ice dam formation.
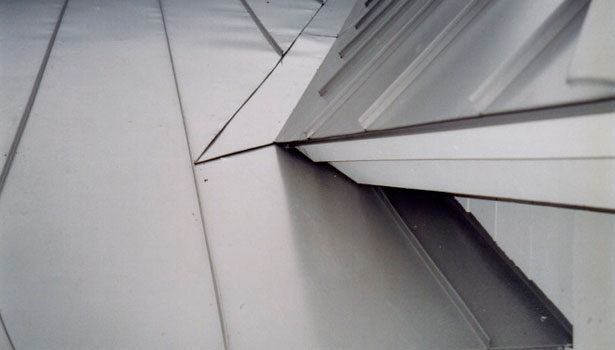
Roofs with multiple planes often have locations where a roof eave and wall terminate at the bottom of a valley.
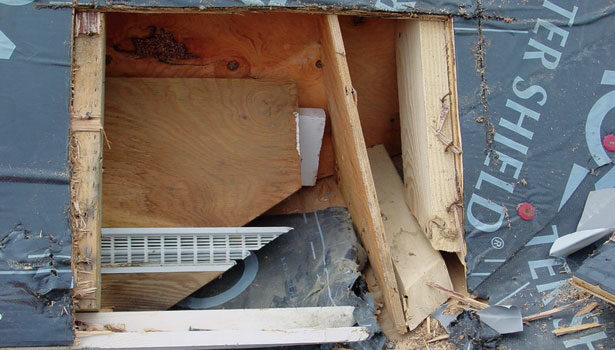
Where eaves, valleys and walls intersect, water can back up and overtop the upslope edge of the roofing at the transition. This is a similar location to the one in photo 3, with the metal roofing and roof sheathing removed.
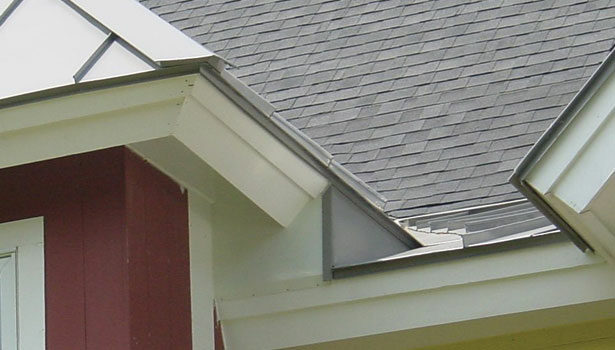
At an eave-valley-wall intersection a box-out can provide a substrate for the ice barrier membrane and covering.






Ice dam-related water leakage continues to plague many steep-slope roofs. Some contractors and consultants we meet while evaluating leakage from ice dams suggest that the water leakage occurs due to material and design limitations, not the roofing installation. Regardless of design and construction, ice dams can form under the right conditions (Photo 1), although the risk can be small at a well designed and constructed roof (i.e., design and construction beyond the minimum code requirements). All roofs in cold regions have a risk of ice dam formation; therefore, roofs must be constructed to resist water leakage from snow, ice and water buildup behind ice dams. Nearly all roofs can be designed and constructed to prevent water leakage from ice dams. In our experience, roofs that leak when ice dams are present typically leak due to basic design and construction errors.
This article focuses on constructing a waterproof roof to prevent water leakage that results from the formation of ice dams. We provide a brief review of ice dam formation; discuss codes and standards related to ice dam protection; and explore design and construction considerations. We do not discuss the important topic of heat loss and ventilation required to minimize the risk of ice dam formation; there are several good papers on the subject1.
This article is based on steep-slope asphalt shingle roofing that is designed and constructed per the 2012 International Building Code (IBC) and current standards. The information herein is also applicable to other steep-slope roofing materials, and projects based on the International Residential Code and other model codes.
Ice Dams
Ice dams form in cold weather when snow on roof surfaces melts and freezes on colder roof surfaces, typically at eaves. Heat loss from the building interior, direct solar radiation and warmer weather all contribute to snow melt. Once an ice dam starts to form, it impedes drainage of subsequent snow melt and rain water. As the water collects behind the ice, it freezes and increases the size of the ice dam laterally along the eave and eventually upslope. This process continues as long as the appropriate weather and water supply exist. When there is a pathway through the roofing assembly, the hydrostatic pressure of the water causes leakage.
Code Required and Industry Standards
A designer and contractor have a minimum obligation to meet the building code, with local amendments. Chapter 15 of the IBC requires:
- "1507.2.4 Self-adhering polymer modified bitumen sheet. Self-adhering polymer modified bitumen sheet shall comply with ASTM D 1970.”
- “1507.2.8.2 Ice Barrier. In areas where there has been a history of ice forming along the eaves causing a backup of water, an ice barrier that consists of at least two layers of underlayment cemented together or of a self-adhering polymer modified bitumen sheet shall be used in lieu of normal underlayment and extend from the lowest edges of all roof surfaces to a point at least 24 inches (610 mm) inside the exterior wall line of the building.”
State codes and local officials often clarify where an ice barrier is required and may increase waterproofing up the slope. Using two layers of underlayment cemented together became a thing of the past with the performance of modern self-adhering membranes.
The requirement that ice barrier membranes meet ASTM D1970 “Standard Specification for Self-Adhering Polymer Modified Bituminous Sheet Materials Used as Steep Roofing Underlayment for Ice Dam Protection” is important because it, among other things, requires testing self sealability and lap integrity under a head of water. In the self sealability test, the membrane is adhered to plywood, two galvanized roofing nails are driven through the membrane and backed out ¼ inch, and tested with 5 inches of water head for three days. Similar testing is performed on a lap.
As part of the building code, the designer/contractor obligation includes using manufacturer’s instructions and referenced industry standards (e.g., 2013 IBC Paras. 102.4 and 1503.1). By extension, some references are adopted by the code. Additionally, a designer and contractor must meet the standard of care for its work (e.g., “the degree of attentiveness, caution and prudence that a reasonable person in the same circumstances would exercise”2). The standard of care obligates a designer/contractor to consider, and implement as appropriate, the industry standards, installation instructions, and practices of those in the industry locally and/or more broadly, even if not identified in the code.
A primary roofing-related standard for steep-slope roofing is The National Roofing Contractors Association’s NRCA Roofing Manual: Steep-Slope Roof Systems (2013). It has recommendations similar to the code requirements — extend the ice barrier 24 inches from the interior surface of the exterior wall. It provides additional guidance regarding where an ice barrier is appropriate:
“Regardless of the type of underlayment required or the roof slope, in locations where the average temperature for January is 30ºF or less, NRCA recommends installation of a water and ice-dam protection membrane.” The NRCA provides a map of the USA, but we note that we see ice dam leakage in locations (e.g., Baltimore, Md.) outside the NRCA recommendation.
“Water and ice-dam protection membranes for downslope perimeters and various flashing locations, including transitions, valleys and penetrations, are recommended in cold regions. In climates where ice damming can be severe, consideration should be given to extending the water and ice-dam protection membrane further up the slope.”
The NRCA also states that “water and ice-dam protection membranes by themselves should not be relied on to keep leaks or moisture problems from occurring,” and “careful consideration of roof insulation, ventilation and project- and climate-specific detailing is vital.” We agree that design and construction to minimize heat loss into attics and provide appropriate ventilation to reduce ice dam formation is important, but the minimum code requirements will not prevent ice dam formation. Therefore, we must rely on the ice barrier membrane as waterproofing, appropriate design and workmanlike construction to protect against ice dams leakage.
The Minimum Ice Barrier Protection
The minimum standard should be the installation of an ice barrier membrane to prevent leaks under reasonably expected service conditions. Critical to the successful performance of the roof is the designer/contractor believing that the ice barrier membrane they are specifying and installing must perform as “waterproofing.” The principles of adhered waterproofing apply. We consider the following:
Expected snow, ice and water buildup: In general, the building code and industry standards do not define all geographic locations and roof areas with increased risk of ice dam formation. This is no surprise because every building has unique circumstances, such as exposure, roof geometry, etc. The design/construction team must identify and address the locations of risk. For example, a roof constructed on the shore of Lake Champlain in Vermont has the same code and industry standard requirements as the same roof constructed on the side of a Vermont mountain at a high elevation with greater weather exposure.
Like location, roof geometry plays an important role in expected ice dam formation. A simple roof with no valleys has less risk than a similar roof with valleys, and a roof with valleys has less risk than a roof with obstructed valleys or pinch points (Photo 2).
Roofing system: Not all roofing systems are equally appropriate for all locations or have the same risk. The appropriateness of asphalt shingles decreases with decreased roof slope and expected snow buildup. Metal roofing (e.g., standing seam) is generally more suitable on lower-slope roofs and on roofs where snow buildup is expected because it sheds snow, provides a less pervious first roofing layer and may have fewer fasteners through the ice barrier membrane. In some instances, the increased water resistance of soldered metal or single-ply roofing may be appropriate.
Ice barrier membrane products and installation: Like most products, not all ice barrier membranes are equal. All ice barrier membranes must meet the requirements of ASTM D1970 to meet the IBC 2012. However, some membranes, compared to other membranes, form more reliable laps, adhere better, seal better around fasteners, are easier to apply at penetrations, are easier to handle, etc. Additionally, some manufacturers have a broader range of ancillary products (e.g., primer, fluid-applied membrane, etc.) and more technical support. The designer/contractor must determine the appropriate product for the application. As a general statement, we recommend:
- Rubberized asphalt-based adhesive over butyl-based where service temperature and compatibility permits. It is our experience that workers achieve higher initial and long-term adhesion with rubberized asphalt membranes; these properties are critical to waterproofing performance.
- Ice barrier membranes that adhere on contact versus membranes that require heat from the sun after installation. Workers can then confirm proper adhesion, waterproof laps, etc. prior to covering the membrane. If moisture collects on the substrate underneath the unadhered membrane surface, it can irreparably damage the bond.
- Ice barrier membranes that are flexible rather than more rigid. More flexible membranes are typically more difficult to install without wrinkles, but are also typically better for establishing initial adhesion and for detailing.
- Primer to improve substrate adhesion. Typically “optional” primers that bind the sawdust and other fine surface contaminants improve bond.
- Mastic/roofing cement at difficult details, especially in areas where snow is expected to buildup. We use mastic/roofing cement at details, to cover "pinholes” in ice barrier membrane at corners, etc. Mastic must be installed over the membrane to allow solvents to off-gas.
- Fluid-applied membrane at difficult details similar to mastic. The fluid-applied membrane is typically installed underneath the ice barrier membrane. It is more expensive, but more durable than mastic.
Substrate preparation and membrane adhesion are critical to the performance of the ice barrier membrane as waterproofing. The following are required for durable and reliable waterproofing:
- Substrate preparation. The substrate, such as plywood roof sheathing, must be properly supported and attached, and have smooth transitions at joints. Roof sheathing that deflects at joints can tear the ice barrier membrane. Uneven substrate transitions or gaps (e.g., 1-inch gap in a valley) do not allow full adhesion and can result in torn membrane and failed seams. At uneven transitions and gaps, we specify sheet metal attached with a tight fastener spacing along the edges (4 inches on center) to limit thermal movement and the resultant “oil-canning” that can cut the membrane.
- Full adhesion. Ice barrier membrane must be fully adhered to keep seams sealed. Adhesion requires two critical steps: a clean and dry substrate at the proper temperature (priming typically increases adhesion), and firmly “pressing” every inch of the membrane into the substrate. In order to achieve full adhesion the membrane must also be fully supported (i.e., no gaps or steps in substrate).
- Reliable seams. The pieces of membrane forming the seams must fully adhered to each other with no pathways for water (e.g., wrinkles). The two pieces of membrane must be firmly pressed together against the substrate. Seams that cross gaps and uneven transitions lack the support necessary to reliably seal the seam.
- Transitions. Substrate gaps commonly exist at transitions, such as valleys and roof-to-wall transitions. Again, it is often necessary to close these gaps with sheet metal. A cant at roof-to-wall transitions improves seam reliability by easing the membrane transition, especially at seams.
- Eaves: The code requires the ice barrier membrane to start at the lowest point on the roof surface (i.e., eave). Starting at the downslope eave edge of the roof sheathing meets this code requirement but is often not sufficient to prevent ice dam water leakage.
We recommend a detail adopted by a leading manufacturer that starts the ice barrier on the vertical surface of the fascia. Install a strip of ice barrier on the roof sheathing that terminates on the fascia face (concealed by the edge metal). Then install the eave edge metal and ice barrier over the initial strip and edge metal flange. Otherwise, water can leak through the sheathing/fascia joint and/or lap joints in the eave edge metal into the soffit and/or building wall (Figure 1). Icicles hanging from a soffit or extending from the siding below the soffit are often a telltale sign that water is leaking into the soffit.
The code requires the ice barrier membrane to extend to a point at least 24 inches from the interior surface of the exterior wall (measured horizontally). One strip of ice barrier that is 3 feet wide may not extend upslope the minimum of 24 inches. For example, a roof eave with a 12-inch overhang, 2-by-6 walls, and 8 on 12 roof slope requires the ice barrier to extend up the roof slope approximately 50 inches measured along the slope.
At roof locations where snow and ice accumulate, such as at the bottom of a valley, expect the ice dams to extend further up the roof eave and extend the ice barrier membrane to meet this challenge.
Terminations at walls: Roof surfaces often terminate at walls (e.g., dormers). The roofing underlayment (ice barrier membrane and other underlayments) must turn up building walls behind the step flashing to prevent water on the underlayment from leaking to the interior below flashing. In areas where ice dams form, the ice barrier should extend up the wall higher than the expected height of snow buildup. Sliding snow can accumulate to great depths at dormers and other obstructions.
Where eaves terminate at building walls, the ice barrier must extend onto the weather-resistive barrier below the eave and the step flashing terminate on the outside of the wall cladding with a kick-out flashing to prevent water flow behind the cladding.
Eave/valley/wall intersection: Roofs with multiple planes often have locations where a roof eave and wall terminate at the bottom of a valley (Photo 3). Water can back up and overtop the upslope edge of the roofing at the transition (Photo 4). Although it is possible to waterproof this condition, the detail is simplified with a box-out that provides substrates for the ice barrier membrane and covering (Photo 5).
Summary
Roofs constructed in geographic regions where ice dams are likely to form should be designed and constructed to limit the risk of ice dam formation and snow, ice and water buildup. Regardless of the design and construction, ice dams can form under the right conditions. Therefore the roofing must be designed and properly constructed with a quality ice barrier membrane where ice dams and snow, ice and water are reasonably expected. The ice barrier membrane is “waterproofing,” and must be designed and installed as such.
Designers and contractors are obligated to meet the building code, manufacturer’s instructions and code-referenced industry standards, and the standard of care for their work. Failure to meet these obligations increases the risk of roofing failures. In our experience, if a dispute arises that involves the roofing, failure to meet these obligations increases the designer’s and contractor’s risk regardless of the cause of leakage.
References:
- Tobiasson, W., J Buska, and A. Greatorex. “Attic ventilation guidelines to minimize icings at eaves.” Interface Jan. 1998: 17-24.
- http://definitions.uslegal.com/s/standard-of-care
Looking for a reprint of this article?
From high-res PDFs to custom plaques, order your copy today!