Straight Green: When Codes Collide
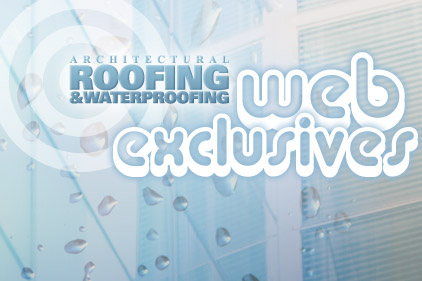
One might expect that the ICC family of codes is well coordinated; however this is not always the case. Energy efficiency in buildings has been, and continues to be, the most important aspect of green building rating systems and energy conservation codes. ASHRAE 90.1 “Energy Standard for Buildings Except Low-Rise Residential Buildings” and the International Energy Conservation Code have significantly increased the minimum requirements for building enclosure efficiency. For exterior walls, this has resulted in a prescriptive requirement for continuous insulation placed within the exterior wall assembly between the sheathing and the cladding. The additional thickness required to achieve the prescriptive R values can be a challenge to building designers, the thicker the insulation, the more difficult to resolve. In this case, thinner is better, and foam insulations are the preferred choice, having greater R value per inch, lower cost, and wider availability than alternatives such as spray foam and mineral wool. ASHRAE 90.1 and the IECC allow any type of insulation to be used in the assembly to satisfy the requirement.
Building codes have addressed foam plastic insulation used in exterior wall assemblies since 2000, when the requirement to test in accordance with NFPA 285 “Standard Fire Test Method for Evaluation of Fire Propagation Characteristics of Exterior Non-Load-Bearing Wall Assemblies Containing Combustible Components” was added. When first introduced into the building code, there were not many exterior wall assemblies that were being designed with foam plastic insulation (with the exception of EIFS), and the requirement was not something most designers ever had to deal with. Because the main constituent of EIFS is foam plastic, the EIFS industry was quick to test their systems to prove code compliance.
The problem now is that there are many exterior wall assemblies being designed and built with continuous foam insulation without having met the testing requirement in Chapter 26 of the IBC, which says, in Paragraph 2603.5.5:
“Test Standard: The wall assembly shall be tested in accordance with and comply with the acceptance criteria of NFPA 285.”
WHAT IS NFPA 285?
NFPA 285 is a fire test conducted with a prescriptive two-story wall assembly with an opening at the first floor to allow fire to propagate upward and across the exterior surface of the assembly. This is a pass/fail test that requires no flame propagation beyond an acceptable distance from the area of flame plume impingement on the exterior face of the wall assembly. There are many building products on the market that have passed NFPA 285, but far fewer wall assemblies have been tested, as the current language in the code requires. And this is the problem.
In a 2010 article titled “Code and Fire Test Requirements for Foam Plastic Insulation Used in Exterior Walls” on the International Code Council’s Online Journal, authors Jesse J. Beitel of Hughes Associates Inc. and Bruce J. Spiewak, AIA, Consulting Architect LLC state the following:
“Even though a specific component of the wall system has met the requirements of NFPA 285, if additional combustible components are added to the wall assembly, then the assembly may no longer meet NFPA 285. For example, if a Metal Composite Material by itself is successfully tested via NFPA 285, and if a CI such as foam plastic is added to the system, the new combination of materials may not meet the Code and the NFPA 285 performance requirements. The new combination wall assembly must be tested.”
Many wall systems manufacturers, contractors, owners, code officials and architects have been going about their daily lives without knowing about this requirement. Buildings continue to be designed and built that do not satisfy this code requirement. How can that be? I asked two building code consultants this question and their answer was simply that code officials are not enforcing the requirement; or at least not strictly. One example given for a recent project involved the building code official accepting NFPA 285 testing for just the foam insulation itself applied to the interior surface of an exterior precast panel assembly. In another, the building code official initially expected to see every exterior wall assembly to be tested. In this example the number of different assemblies with foam insulation was significant. Upon explaining to the code official that the cost of this testing would be prohibitively expensive, he reversed his ruling, and declared that this was not the intent of the code requirement, as he interpreted it.
FOLLOW THE CODE (OR NOT)?
Continuous insulation is now being integrated into many exterior wall assemblies to satisfy energy code requirements; masonry veneer (brick, stone and CMU), metal plate wall panels, metal composite wall panels, formed metal wall panels, precast wall panels (sandwiched or applied to the interior face), fiber cement siding, etc. In strict accordance with the building code, if foam insulation is used, every one of these assemblies, in every possible combination of components, must be tested. So what is the liability involved in ignoring this requirement? In an excellent article “Architect’s Duties” by Lonnie Johnson, attorney with Clendening, Johnson and Bohrer, P.C., he writes:
“Consider, for example, Center Court which involved a lawsuit by an owner against an architect where the architect’s design contained a number of building code violations [viii]. The owner presented undisputed evidence that the architect’s design violated the applicable building codes. The architect argued that he had considered the applicable code and, in his judgment, created a design that complied with the code. Nonetheless, the court granted judgment to the architect with respect to certain claimed building code violations because the owner failed to establish that the architect violated his standard of care with respect to the building code issues. The owner’s evidence of the code violation did not, in and of itself, establish a breach of the architect’s standard of care. The court relied upon evidence produced by the owner’s own expert as well as other experts that differences of opinion as to interpretation and application of building codes “quite often” arise on construction jobs [ix]. The court agreed, finding no evidence that the architect violated his standard of care with respect to interpreting the building code and creating the design.”
In this case, even though the architect was contractually obligated (as is typically the case with standard forms of agreements for architectural services) to design the building in accordance with the building code, the owner was unsuccessful in persuading the court that the architect was negligent. The author concludes that a design professional:
“… is not necessarily required to create designs that necessarily comply with the building code as courts recognize that building codes are often difficult to interpret, even if established, proof of a building code violation in a designer’s plans, specifications or designs, is not sufficient to establish negligence on the part of the designer because it does not address the standard of care issue.”
In another example, from the book Legal Aspects of Architecture, Engineering and the Construction Process by Justin Sweet and Marc M. Schneier, an architect was sued for designing a … condominium building that did not have the required number of fire exits in accordance with the local building code. Prior to construction, the architect’s design was reviewed and approved by the chief code enforcement officer as having been in compliance with the code, even though different from the strict letter of the code. During the trial, the architect produced expert witnesses that testified that the building, as designed by the architect was safe and satisfied the intent of the building code. The court concluded that:
“… the architect had complied with the code, because the chief building inspector and the chief code enforcement officer stated the design did comply. This was relied upon by the architect, and the building was constructed with the approved design. The court noted that even though a code could be interpreted in more than one way, the law will follow the interpretation of the agency that has authority to implement the code.”
CONCLUSION
Adding continuous foam insulation within an exterior wall assembly is becoming de rigueur as owners and designers look for the best way to satisfy newly implemented energy code requirements. Building code requirements that these assemblies be tested in accordance with NFPA 285 are largely being ignored, and unenforced. The National Institute of Building Sciences recognizes that the intent of foam insulation exterior wall assembly NFPA 285 testing and the written building code requirement, are out of alignment. To bring them into alignment, NIBS released a Request for Letters of Interest and Statements of Qualification in June, 2011 seeking a “fire protection engineer/consultant to provide assistance to the BEC National Task Group to clarify the risk and appropriate test criteria for foam plastic insulation in exterior wall assemblies.” The RFQ states:
“There is much confusion amongst architects, engineers and contractors over the requirements in the International Building Code regarding FPI and its application in exterior wall assemblies. Local code officials weighing in on this matter appear to cloud the issue even further by not providing a consistent interpretation across jurisdictions as to what is required, particularly as it relates to IBC 2603.5.5. With continuous FPI on the exterior of the weather barrier increasingly becoming a more cost effective means to deliver maximum R value, it is this BEC National Task Group’s mission to research the genesis of the code requirement and past losses, evaluate the applicability to current wall construction techniques and other test methods referenced in the IBC and advocate for a change to the language in Chapter 26 of the IBC as it relates to FPI in exterior wall applications.”
NIBS was hopeful that a recommended code revision would be submitted to the ICC in December, 2011, for consideration into the 2012 IBC code revision cycle, and incorporated into the 2015 IBC. This did not happen, unfortunately, and the next opportunity for the recommendation to be submitted would be for the 2015 revision cycle, for adoption into the 2018 IBC.
In the meantime, architects and owners would be well advised to discuss the issue with the code enforcement official well in advance.
Looking for a reprint of this article?
From high-res PDFs to custom plaques, order your copy today!