Understanding Wind Uplift Ratings
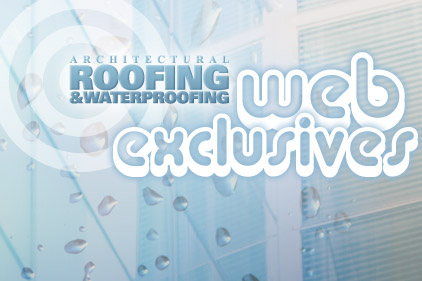
What is an FM Approvals wind test, and what do the various wind uplift ratings mean? This question is frequently asked, but often answered incorrectly.
Before we can answer the question, however, we must first define wind uplift.
Roof damage caused by wind occurs when the air pressure below the roofing assembly is greater than the air pressure above the building's roof. As wind flows over the building, the pressure directly above the surface of the roof decreases. At the same time, internal air pressure increases due to air infiltration through openings, cracks, etc. The result is a net upward force on the roofing system. This force is referred to as wind uplift.
Let's start by clarifying who FM Approvals is and their role in low-slope roofing. FM Approvals is a nationally recognized testing laboratory that tests and certifies building materials, fire protection and electrical equipment that can help prevent or reduce property damage. Those products and services that meet FM Approvals' rigid testing criteria become FM approved and bear the "FM" diamond certification mark.
The company is a business unit of commercial and industrial property insurer FM Global, which insures more than one-third of Fortune 1000 companies and similar-size organizations worldwide.
Based on decades of experience, FM Approvals has developed many test standards and industry protocols on various property conservation topics. While this article is focused on wind testing, FM Approvals also tests roofing systems for resistance to interior and exterior fire exposure, hail resistance and long-term weather resistance, as well as other physical properties.
Common Misconceptions
![]() |
This wind uplift test in progress shows a system under pressure. The membrane is beginning to lift in repsonse to increased air pressure from below. (Photo courtesy of OMG Roofing Products) |
FM Approvals' work has driven the evolution of many types of roofing systems and certainly has played a big role in the development of the high-performance fastening systems we use today.
Neither FM Approvals nor FM Global are building code-making bodies, but FM-approved roofing systems are often specified, so it's important that specifiers and designers understand FM Approval's role and the wind ratings. One common misconception is the belief that FM Approvals' windstorm classification ratings such as 1-60, 1-90 or 1-120 correlate to wind speeds of 60, 90 or 120 miles per hour (mph). Building owners and some specifiers and designers don't realize that the ratings apply to uplift pressures in pounds per square foot (psf), not wind speeds.
Furthermore, the roofing designer or specifier sometimes assumes if there is a design wind speed requirement of 90 mph, then the roof system must have a 1-90 rating, which is not always true - at least not for the reason they think (maybe for tall buildings, or if other factors exist).
The second most common mistake a designer or specifier may make is concluding that wind speed is the only factor used in the equation to determine which FM Approval rating is needed. For FM Approvals (as with the American Society of Civil Engineers, or ASCE), geographic location plays a significant role in system level selection.
Consider the example below of how FM Approvals' windstorm classification ratings are used correctly in roofing design.
The first step is to verify that the building in question is indeed insured by FM Global. Once that has been confirmed, a variety of data must be gathered about the building and the geography, such as:
- The building's overall height.
- The terrain surrounding the structure.
- The type of roof deck on the building.
- Whether or not the existing deck meets Factory Mutual minimum standards.
- Whether or not the building is a "special use" facility such as an airplane hangar, a hospital or a facility with many large dock doors, etc.
- Whether or not the building has parapet walls, and if it does, their height.
It should be noted that this information is needed if using ASCE 7 to determine the uplift resistance needed as well. FM Global has developed property loss prevention engineering guidelines for determining uplift pressure based on ASCE 7.
These and other factors are used in conjunction with FM Global Property Loss Prevention Data Sheet 1-28, titled "Design Wind Loads," to establish the uplift forces on the specific building. The wind loads will vary in the corners, perimeter and field of the roof. While data sheet 1-28 will determine the specific "size" of the corner and perimeter zones, data sheet1-29, titled "Roof Deck Securement and Above-Deck Roof Components," will explain how to properly fasten the roof system in these high load areas. Recent revisions to Data Sheet 1-29 significantly change the recommendations of compliance for some types of roof systems.
Let's assume that the calculations for our building require a roof that can withstand 23 pounds per square foot of uplift force in the field of the roof. Because FM
Approvals requires a 2:1 safety factor, roofs with field of roof uplift forces of 30 pounds per square foot are the maximum for 1-60 ratings, and 37.5 pounds per square foot are the maximum for 1-75 ratings, etc. In this scenario, our building, which is designed with 23 pounds per square foot of uplift, would require an FM Approved Class 1-60 system design, and follow the requirements of data sheet 1-29 for corner and perimeter enhancements.
![]() |
Pictured here are the pressure regulator and manometer at the OMG test facility. |
As stated earlier, FM Approvals' requirements are specified carte blanche by many designers on buildings that are not FM Global insured. The assumption is that such systems are safe and can reduce the designer's or specifier's liability. However, in many instances these non-FM Global insured buildings do not meet FM Approvals' minimum requirement for roof decks, etc., yet the designer still calls for an FM-approved system. A perfect example of this occurs frequently on the West Coast, where half-inch plywood is commonly used for roof deck construction.
Half-inch plywood does not meet FM Approvals' requirements regardless of the roof cover type. If a building is FM Global insured and has a nonconforming deck type (such as half-inch plywood), FM Global will work with the building owner/designer to find an acceptable roof cover for that project. In general, FM-Approved decks include:
- Steel - 22 gauge and heavier.
- Structural concrete - minimum 2,500 psi.
- Wood - 3/4-inch minimum fire retardant treated plywood, or minimum nominal 2-inch thick fire retardant treated dimensional lumber.
- Cementitious wood-fiber, such as Tectum.
- Lightweight insulating concrete.
- Fiberglass-reinforced plastic.
In 1989, Hurricane Hugo ripped through the Carolinas, leaving miles of devastation in its wake. Then, in 1992, Hurricane Andrew pounded South Florida like few storms ever before. The ripple effect of these hurricanes forever changed the face of the commercial roofing industry. As a legacy to these storms, roofing manufacturers continue working to develop roofing systems that will economically meet new, more stringent, FM Approvals and FM Global wind uplift standards, enhanced windstorm classifications, and Dade County, Florida test protocols.
A spokesman for FM Global reports that they are unaware of any roof systems that were approved on the 12-foot by 24-foot test frame that failed during Katrina. The failures that did occur to approved roof assemblies were due to damage from windborne debris or inadequately secured corners and perimeters.
For a roofing system to qualify for FM Approval, the system must be tested by the laboratory to its product testing standards. The specific test that pertains to wind uplift utilizes a test apparatus designed by FM Approvals. For mechanically attached single-ply roofing systems, the test involves building a roof assembly on a test frame that measures 12 feet by 24 feet.
![]() |
OMG Roofing Products conducts a wind uplift test on a 12-foot by 24-foot section of a system at its dedicated testing facility in Agawam, Mass. |
The test frame has the appropriate roof deck attached to supports. Insulation (any type) is then fastened to the deck and the single-ply membrane is secured over the insulation to the deck. The test frame is clamped to a pressure vessel that is pressurized to 30 psf and held at that level for one minute. Assuming that the roofing system remains undamaged at the end of the first minute, the pressure is increased to 45 psf and held for another one-minute period. This process is repeated in 15 psf increments until any component of the system fails. The approval for that assembly is established at the level preceding failure. The minimum wind approval rating is 60 psf. For example, if the pressure level was at 105 psf when the failure occurred, the Approval level would be set at the preceding level or 90 psf, giving the assembly a 1-90 rating.
Failure can involve any number of events, such as delamination of the roof seam, membrane tear, screw pullout, etc. While the test is conducted on a product made by a particular deck manufacturer, extension of these approvals to other approved decks (of comparable or greater thickness, depth, rib configuration and yield stress, used within the limits of the approved spans) made by other manufacturers is common based upon favorable comparative testing of the appropriate fasteners for the respective deck types. For other steel decks, pullout tests would not be required. For other deck materials (say, wood) they would be needed to confirm performance.
For fully adhered single-ply systems as well as for multi-ply systems, the testing is conducted the same way, with the only difference being the size of the test frame. For fully adhered single-ply systems the test frame is 5 feet by 9 feet if a rating of Class 1-90 or below is desired. If the client desires a higher rating, the test is conducted on the 12-foot by 24-foot test frame.
It is important for building owners and designers alike to understand that FM Approvals ratings do not correlate directly to miles per hour of wind speed, and that understanding FM Approvals testing procedures and windstorm classification ratings will help avoid the many potential problems associated with wind uplift, one of the most common enemies to consider when designing any commercial roofing system.
Make Sure Building Owners and Contractors Know What to Expect
Below are some of the topics that roofing contractors, building owners and specifiers should discuss. Having these discussions early in the process could save you considerable time when your project comes to fruition:
- Is the building FM Global insured? If the building is FM Global insured, make sure the system that is recommended meets the proper windstorm classification and contact the local FM Global office prior ordering material or starting any roofing work.
- Does the recommended system meet all local building code requirements in addition to the FM Approvals requirements and FM Global data sheet recommendations?
- Understand that roofing manufacturers' warranties do not acknowledge or imply compliance with FM Approvals ratings nor building codes.
- Make sure you know what type of deck (gauge, depth, rib configuration and yield stress), deck span and deck securement the facility has and that the building meets FM Approvals requirements.
- If an FM-approved rated system is required, discuss the options with the membrane manufacturer. In many instances, manufacturers have approval ratings that the contractor may not be aware of, which could save you lots of money in terms of labor costs.
Looking for a reprint of this article?
From high-res PDFs to custom plaques, order your copy today!