Environmentally Responsible Design Is Walk in the Park
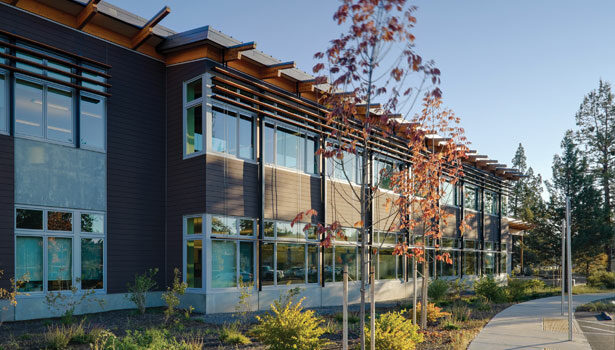
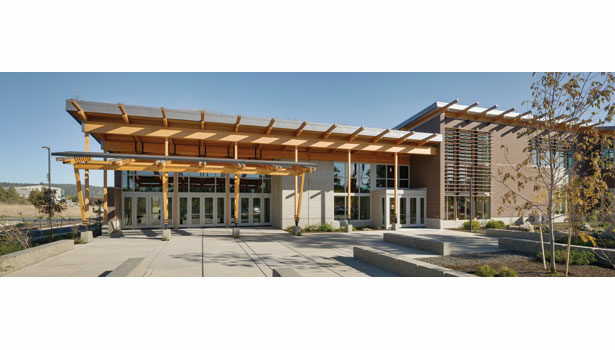
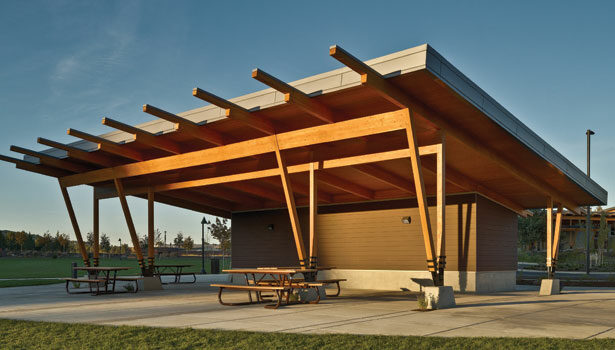
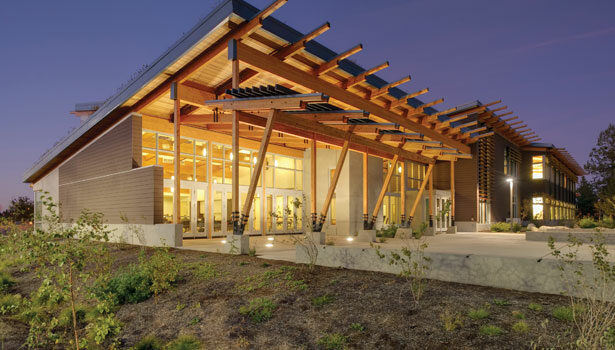
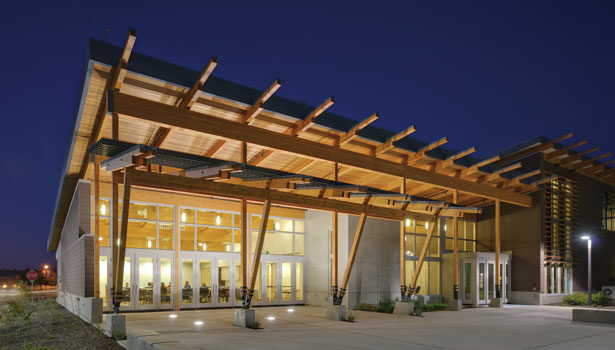
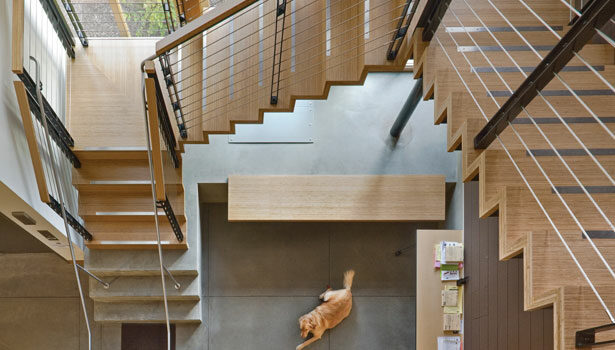
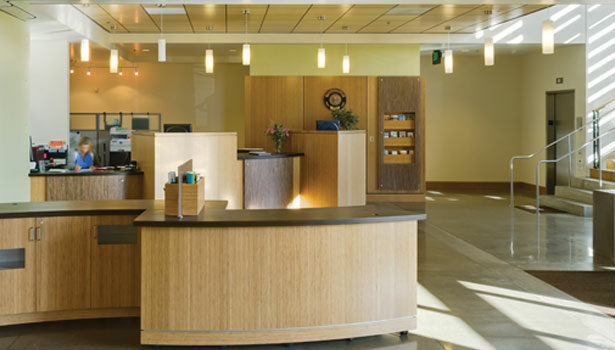
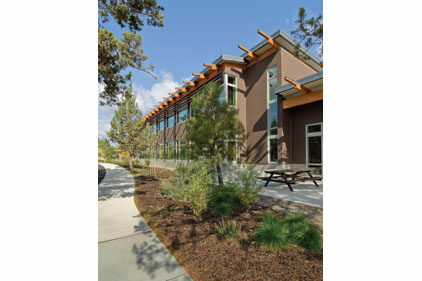
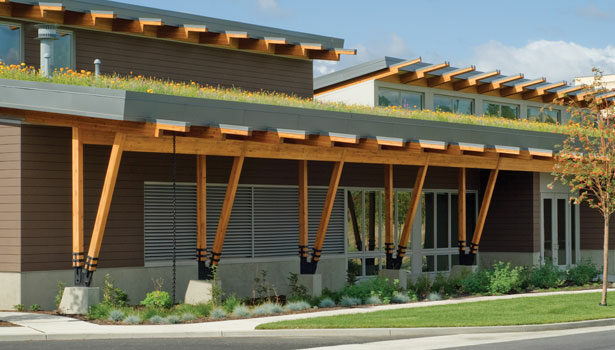
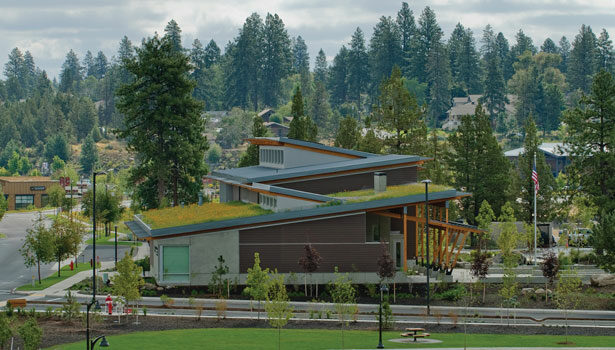










Environmental responsibility is a primary value for the Bend Park & Recreation District, and it was a critical element in the design of the LEED Gold-certified administration building by Opsis Architecture. The project offers a demonstration of how manmade and natural elements can be brought together to blur the boundaries of indoor and outdoor spaces while promoting environmental stewardship.
The new administration building, located on a 14-acre park in Bend, Ore., provides office space for current staff and allows for the department’s anticipated growth over the next twenty years. In keeping with the Bend Park & Recreation District mission, the administration building project is committed to sustainability and respect for the surrounding landscape. Mixing the indoors with the outdoors was integral to the overall design.
“Early in the design process the building committee outlined its desire that the facility respect and integrate with the beautiful riverfront site,” says James Meyer, partner at Opsis. The site, in the Old Mill District area, was selected due to its visibility and central location; both were ideal for serving the community and the district at large.
“Maintaining a tie to the architectural fabric of the Old Mill District, the building’s design is intended to present the visitor with a friendly and welcoming ‘park-like’ experience,” says Jason Miller, senior associate at Opsis. “Public indoor and outdoor spaces were important features to the overall design, making this building within the park a hub for community congregation and local events. The facility’s design is intended to demonstrate the district’s progressive values of environmental and community stewardship, with humble regional charm and a truthfulness of expression.”
In an effort to respect the landscape, existing trees and groundcover were maintained as much as possible. The administration building project preserved 377,836 square feet of vegetated open space, 345 percent more than is required by the local zoning code. The project also included the restoration of the native habitat along the Deschutes River.
Onsite stormwater is collected, treated and infiltrated by an expansive 6,000-square-foot green roof, a series of bio-filtration basins and rock trenches designed for infiltration. “Personally, my most favorite sustainable design feature is the green roof,” says Miller. “Located over the portion of the building which houses the public areas, including the lobby and large community room, this broad lower roof plane tilts upward, increasing access to river and mountain views from the interior. But perhaps more importantly, the angle of the roof exposes the entire surface of succulents and wildflowers to a very public view from the street. In a real sense, it provides the community with a learning opportunity in sustainable systems.”
In addition to using native plantings in the landscape, the project employs a drip irrigation system to reduce water use. Waterless urinals and low-flow fixtures further reduce water use within the building. These efforts result in a water savings of 45 percent, or approximately 85,500 gallons every year.
“Another key feature in the project is the specific building response to the site orientation,” says Meyer. “The north building façade is composed primarily of solid, highly insulated walls with limited glazing areas. On the south side, the building’s glazed walls open to spectacular views to the river and allow sun to penetrate deep into the office spaces while providing summer shading through the use of exterior trellis components.”
Besides providing energy efficiency, the orientation of the building also supplies a sense of organization. “One of the most challenging features of the project was to design a facility that invited the community to use the building while at the same time created highly functional office space,” continues Meyer. “This was accomplished by organizing the uses in a manner that allowed office portions of the building to be closed while community activities in other areas could be going on. To this end, the western portion of the building contained the large community room, fireplace lounge, restroom facilities and the large outdoor terrace. Two main entries were created — one from the south and one from the north — to further offer easy access to the community.”
Thirty-seven percent building energy efficiency is achieved through the building envelope and mechanical systems. The high thermal performance exterior envelope is paired with a mixed-mode natural ventilation system, radiant/chilled floor slab for heating and cooling, two high-efficiency condensing boilers, a solar hot water system, and energy-efficient lighting with occupancy and daylight sensors.
Due to the radiant floor system, though, not every step of the design process was blue skies. “Probably the greatest challenge presented to the team came during the LEED construction submittal review in which the Energy and Atmosphere (EAc1) prerequisite credit was denied,” says Miller. “This was due primarily to the complexities involved with modeling a radiant system, which yielded results that could be falsely interpreted in the energy model. Without satisfaction of this prerequisite, project LEED certification would not have been possible. To address the issue, the team provided information to address the reviewer’s issues primarily concerning fan power, system zoning, outside air rates and heating energy consumption. In addition, the energy model was modified to make the baseline and proposed cases function as accurately as possible to the applicable system types. The project was ultimately awarded LEED-NC v2.2 Gold certification with 43 points.” These efforts are estimated to result in an energy cost savings of more than $29,000 a year. Additional energy consumed by the building is supplied by green power.
Construction waste for the project was tightly managed, allowing more than 88 percent, or 159 tons, to be diverted from landfills. Juniper trees onsite that had to be removed during the project were harvested, milled onsite and reused as custom juniper woodwork in the building’s interior. From the structural steel to the toilet partitions, the building incorporates a significant amount of recycled materials. Based on cost, 19 percent of the materials used on the project were recycled, reducing the impacts that result from the extraction and processing of virgin materials. The selection of local materials was also a high priority for the project, reducing the impact from transportation and supporting the local economy. More than 40 percent of the materials used in the project were extracted, processed and manufactured within 500 miles of the project site. Door frames, stair treads and casework are made from bamboo, a rapidly renewable resource.
Extensive daylight and views contribute to the indoor environmental quality of the administration building. Natural ventilation enhances the indoor air quality and allows building occupants a high degree of control over their thermal comfort. Low-VOC adhesives, sealants, paints and carpets were also used to maintain the air quality.
“Through this process an entire community has felt a sense of ownership and a satisfaction that the mission of stewardship is represented in the area’s first public LEED-certified building,” says Meyer.
Miller agrees. “When client satisfaction is transcended and a real sense of pride and ownership develops, that’s one of the highest complements an architect can receive — you know you got it right.”
The above information was provided by Opsis Architecture.
Bend Park & Recreation District Administration Building
Submitted by: Opsis Architecture Date Completed: October 2010 Size: 21,326 square feet Location: Bend, Ore.
Architect: Opsis Architecture Partner-in-Charge: James Meyer Client: Bend Metro Park & Recreation District MEP Engineer: PAE Consultants Structural Engineer: Madden & Baughman Civil/Geotechnical Engineer: MGH Associates Construction Manager: Skanska USA
Materials Flooring: Mannington Commercial (carpet); daltile (ceramic tile) Ceiling: Armstrong (acoustical ceiling tile); Tectum (acoustical ceiling panels)
Wood: Forest Grove Lumber Company Roofing: The Bryer Company (metal roof panels); AEP Span
Insulation: GreenFiber (insulation); Insulfoam (expanded polystyrene); Interior Finishes and Furnishings: Herman Miller (office furniture); Bretford (conference tables); Baltix Furniture Inc. (work surfaces); Modernfold Inc. (partitions); Abet Inc. (laminate); PaperStone (countertops); Smith & Fong Plyboo; Forbo Paints and Wallcoverings: Rodda Paint Energy Efficiency: WattStopper (occupancy and daylight photocell sensors)
Building Envelope: Cascade Steel; Premier Building Systems (SIPs); Plumbing Fixtures: Sloan (flush valves and faucets); Kohler (waterless urinals); Powers (showerheads) Landscaping: Specialty Soils; Saris Cycling Group (bicycle racks); NW Horticulture; Round Butte Seed Growers (erosion control seed) |
|
Looking for a reprint of this article?
From high-res PDFs to custom plaques, order your copy today!