How to Properly Determine Moisture Content in Roof Systems
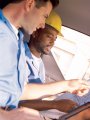
The roofing industry is now at a point where we should collectively define a uniform standard for the determination of moisture content in roof systems. It is time to move past the days of the “educated toe,” i.e., subjective claims of how the system felt as it was walked across. A standard would benefit all sectors of the industry preventing frivolous lawsuits and unsubstantiated claims driven by the pursuit of profit. When done properly, the determination of moisture content can be conducted with advanced technological equipment, laboratory testing and scientific equations. The process has advanced to the point where moisture analysis can be objective and reliable.

Proper moisture analysis includes a combination of both nondestructive and destructive methods of testing. Investigations that incorporate only one of these methods are insufficient and lack credibility. The technology of the moisture testing equipment that is currently used to conduct nondestructive tests has evolved in recent years to the point where it now provides analysis (a snapshot) of the overall roof conditions of large areas in a quick and efficient manner. Even with these advancements, destructive testing - coupled with gravimetric tests - is required to verify the conditions observed by the moisture analysis equipment.
There are three types of nondestructive testing equipment: impedance/capacitance, infrared and nuclear. One of these methods, or a combination thereof, should initially be used to obtain an overall assessment of the roof system. Technicians trained in the proper use of the testing equipment and employed test methods should conduct the testing.
Impedance/Capacitance
Impedance or capacitance moisture testing is conducted using a variety of small, hand-held meters which, when set over the roof membrane, emit low-frequency electronic signals from rubber electrodes located at the base of the instrument. These types of meters typically determine if a specific roof area is wet or dry. They do not have the capacity to measure the percentage of moisture present. Dry readings are projected at points where the electrodes are insulated from one another and there is not a complete electrical circuit. The electrical conductance is greater at wet areas, which provide a complete electrical circuit.
Impedance testing can be conducted in a pattern or at various points throughout the roof area. A higher number of readings provides a more cohesive moisture determination. The testing cannot be completed over wet or ponded areas and modified instruments are typically required for EPDM roof systems.

Thermal masses, or “hot spots,” are not always an indication of moisture presence. They can be illustrated at under deck heating or cooling vents, venting of hot fumes, moisture on the roof surface (ponded water), or at points of heavy gravel application. Most infrared cameras require clear weather conditions for an extended period prior to and during the testing. This typically includes no recent or current precipitation, heavy cloud cover or windy conditions. Any or all of these conditions could distort the infrared findings.
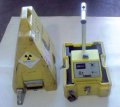
Nuclear thermography is conducted using a nuclear scanning meter that emits neutrons from a radiation source from the scanning meter down through the roof assembly. The emitted neutrons that encounter hydrogen atoms in the roof assembly are slowed down and bounced back to the counting detector within the scanning meter. Higher levels of slowed neutrons are recorded at wet areas because water contains a significant amount of hydrogen atoms. The recorded reading is an average of the total roof assembly.
Generally, nuclear scanning can be completed to depths of as much as 7 inches and testing can be conducted in areas of ponded water. Testing is conducted over the entire roof area by sectioning the roof into grids (5 feet by 5 feet or 10 feet by 10 feet) and recording the readings at each of these locations.

After a complete moisture analysis of the roof is conducted and all of the potential wet areas are marked on the roof plan, it is time to determine the true moisture content of the roof system. This is done by extracting test samples or core cuts from the roof area. Core cuts are conducted in a moisture analysis because all of the aforementioned test methods have their limitations. Moisture identified by nondestructive moisture testing is relative and must be quantified by a combination of physical core cuts and gravimetric analysis.
In the moisture analysis procedure, the core cuts are extracted to determine both the construction and moisture content of the existing roof system. For these purposes, extraction of the core cuts can be completed in the following manner for all types of roof systems:
1. Identify the appropriate location of the core cut. The proper area should be representative of the entire roof area construction. Do not take a core cut from a previously repaired area.
2. A core cut should be extracted from those areas determined to be dry and areas found to have varying levels of moisture presence: low, medium or high. Facilities with multiple roof areas and/or multiple roof systems require core cuts from each roof area.
3. Identify the locations of the core cuts on the roof plan.
4. Use a template and measure the area to be cut. Core cuts can range from 2 inches by 2 inches to 12 inches by 12 inches, depending on the amount of physical property testing that is required.
5. Following the established pattern, cut the membrane, as well as any insulation and underlayments to the structural deck. Single-ply systems can be cut with scissors. Bituminous roof systems require a box cutter knife or hatchet.
6. Remove all roof system components (membrane, insulation and underlayment) from the opening.
7. Photograph the system components and structural deck substrate.
8. Record system construction components, identifying the method of attachment of each component, including:
- Deck type.
- Underlayment (if used).
- Insulation type, thickness and condition (each layer).
- Method of insulation attachment (each layer).
- Membrane type, thickness and condition.
- Method of membrane attachment.
- Type of surfacing and method of attachment.
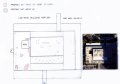
After proper repair of the core area is completed, the core samples should be separated and placed in a watertight container and immediately transported to an approved testing facility for gravimetric testing.
Moisture determination cannot be established solely on a visual (subjective) inspection of the materials. Standard procedures should specify that the exact moisture content of the material is determined through the use of gravimetric testing. Gravimetric testing is conducted by cleaning off the core sample components of debris and placing each component into an identical container. The core component and container is then weighed in its “wet” state. The drying process is accomplished by placing the individual component into a convection chamber for 24 hours at 230°F (114°C). After the drying process - which may include additional drying time - the samples are reweighed while still in the container. Moisture by weight is determined for each tested component by using the following formula:
Dry Basis, % of moisture=weight of moisture/oven dry weight=total weight-oven dry weight/oven dry weight
In the early 1990s, Wayne Tobiasson published a study entitled “New Wetting Curves for Common Roof Insulations,” which indicated that insulations retained their thermal capabilities at up to 80 percent of their original dry content. Through the use of a Thermal Resistance Ratio (TRR), which is determined by dividing the material’s wet thermal resistivity by the material’s dry thermal resistivity, each insulation’s moisture content capacity was determined. When an insulation’s percentage of moisture content enables the TRR to fall below 80 percent, the insulation is determined to be wet.
The following chart provides moisture content by percentage of volume for common commercial low-slope insulations. If the percentage obtained in the gravimetric testing is equal to or greater than the percentage of volume listed in the chart, the tested insulation should be considered wet.
The results of the moisture analysis should be provided in report form. A roof plan accurately identifying all wet areas should be included with a report of findings, test analysis and recommendations. All wet insulation should be removed from the system to deter possible structural deck damage. If the cost of insulation removal exceeds the point of diminishing returns, full roof replacement should be considered.
Material % of dry weight % of volume
Fiberboard . . . . . . . . . . . . . . .15 . . . . . . . . . . . . . . .4.4
Perlite . . . . . . . . . . . . . . . . . .17 . . . . . . . . . . . . . . .2.7
Fibrous glass . . . . . . . . . . . . .42 . . . . . . . . . . . . . . .6.2
Cellular glass . . . . . . . . . . . . .23 . . . . . . . . . . . . . . .3.1
Gypsum . . . . . . . . . . . . . . . . .8 . . . . . . . . . . . . . . .7.0
Expanded Polystyrene . . . . . .383 . . . . . . . . . . . . . . .6.1
Extruded Polystyrene . . . . . . .185 . . . . . . . . . . . . . . .5.9
Isocyanurate . . . . . . . . . . . . .262 . . . . . . . . . . . . . . .8.8
Foamed-in-place urethane . . .130 . . . . . . . . . . . . . . .6.5
Looking for a reprint of this article?
From high-res PDFs to custom plaques, order your copy today!