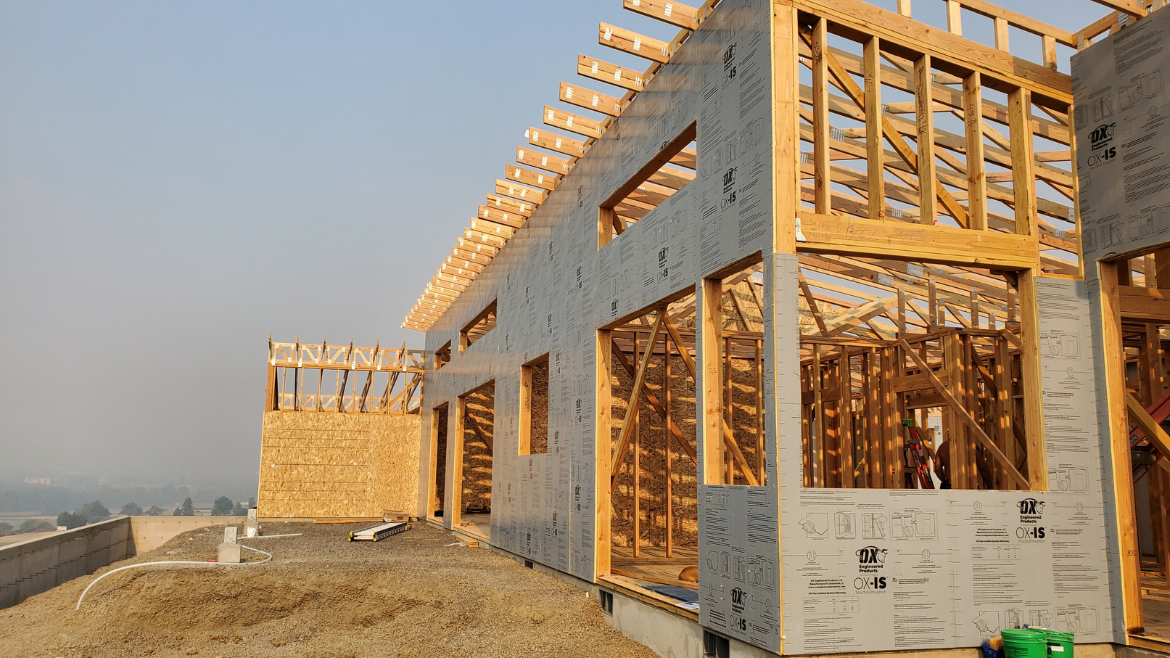
All photos courtesy of OX Engineering Products
Solutions for Structural Strength, High R-Values, and Year-Round Thermal Performance
Professionals are looking for high-performance, integrated solutions that meet the needs and requirements of any climate zones
Temperatures are rising across the globe, and summer heatwaves are increasing in frequency and intensity. The hottest regions are regularly sustaining temperatures of more than 100 degrees Fahrenheit. Persistent and escalating heat is demanding a reassessment of how we design our cities, construct our buildings, and manage resources to adapt to these conditions.
However, the United States offers a diversity of climate zones, and the building materials used on homes and buildings must not only withstand ordinary wear and tear but also perform consistently through every season. The development of “all-weather sheathings” that can handle temperature extremes without compromising structural integrity or energy efficiency are booming in popularity.
In addition, the 2021 International Energy Conservation Code (IECC) includes changes to improve energy efficiency in a wide variety of structures, and insulated sheathing helps to satisfy these new requirements. And contractors, installers, and homeowners are looking for high-performance, integrated solutions that meet the needs and requirements of any climate zones.
Integrated Insulation Solutions
One way to enhance thermal efficiency across the entire building envelope is by incorporating continuous insulation (CI) in building designs. CI minimizes thermal bridging, a process where heat travels through conductive building materials such as metal or wood studs, leading to energy loss. By reducing or virtually eliminating these thermal bridges, continuous insulation helps to maintain consistent interior temperatures, resulting in a more comfortable indoor environment and less reliance on heating and cooling systems.
Some products take the savings even further. For example, structural insulated sheathing solutions that come in 4-in-1 options. Often times, these integrated products combine structural sheathing, continuous insulation, an air barrier, and a water-resistant barrier in a single product. This comprehensive approach allows builders to streamline the construction process while achieving superior thermal performance. This saves on labor and the amount of separate building materials that construction managers need to purchase.
From a performance perspective, the continuous insulation layer within the OX-IS material helps to create a tighter building envelope. This significantly reduces heating and cooling costs, often by an impressive 20-40 percent. The resulting energy savings for owners over the course of a building’s life span are significant. With R-values ranging from R-3 to R-10 depending on the thickness, structural insulated sheathing can be an ideal solution for various climate zones. This is particularly true when builders combine the integrated material with separate forms of thermal protection, such as spray foam or batt insulation.
A couple of key points to remember.
R-value quantifies a material's or assembly's resistance to heat transfer. The more layers of insulating materials, the higher the R-value, and the better the thermal performance. Conversely, U-value represents the overall heat transfer coefficient (expressed in watts per square meter per kelvin). Essentially, it is the inverse of the R-value, and both are important for builders and specifiers to take into consideration.
A higher U-value means that a wall assembly is less equipped to resist heat flow, indicating a lower level of insulation within the wall assembly. A low U-value (or high R-value) will deliver better insulation performance and energy savings throughout a building’s life span. In building design and construction, these values help paint a more comprehensive picture of how well an entire building envelope system will perform from a thermal perspective, taking into account the combined properties of all materials and layers within the structure.
Understanding these measurements and wall system performance equations, construction professionals can use structural insulated sheathing to meet modern day energy codes and standards. In addition to its insulating properties, when builders choose integrated structural insulated sheathing, it acts as an airtight barrier, effectively reducing air infiltration. This means less energy is needed to maintain desired interior temperatures, further improving energy efficiency. With these combined benefits, insulated sheathing is an ideal choice for builders looking to meet or exceed energy efficiency standards while delivering enhanced comfort and long-term durability for the structure for homeowners.
In the (Climate) Zone
A building’s energy efficiency requirement will vary by location, as defined by the International Energy Conservation Code (IECC) zones. These zones dictate minimum requirements for insulation, windows, and other building components to optimize energy performance in each specific climate. Climate zones are defined by temperature, moisture, and location. The IECC uses a numbering system for its climate zones, with 1 ranking as the hottest climate, and 8 being the coldest.
- Hot-Humid Zones (1-3): From hot, humid areas in southern Texas to hot, dry areas in the Southwest and mixed-humid areas in the Southeast, code requirements for insulation are set in place for buildings to resist humidity, reduce heat gain, and protect thermal efficiency. As excess moisture in the air can lead to mold and structural damage, these climate zones place a heavier focus on vapor barriers within the insulation system to prevent excessive moisture build up. For above-grade 2x4 wood-framed walls in zones 1 and 2, the prescriptive minimum R-value is 0 + 10 ci, meaning the requirement for cavity insulation is 0 and for continuous insulation is 10. For basement walls, slabs, and crawl spaces, zones 1 and 2 do not require insulation. For zone 3, above-grade 2x4 walls require 13 + 5 ci and an R-value of 5 in basements and crawl spaces, but nothing for slabs.
- Mixed and Cold Zones (4-5): The pacific Northwest, Midwest, and much of the Great Lakes region require higher insulation levels to maintain temperatures during the colder months, which requires managing moisture and heat resistance. Zones 4 and 5 come with a prescriptive minimum R-value of 13 + 10 ci for 2x4 wood above-grade walls, and R-10 for basements, crawl spaces, and slabs.
- Very Cold to Subarctic (6-8): These climate zones cover parts of the northern Rockies and Great plains, northern parts of the U.S., and Alaska. These areas carry the highest insulation demands to aid in protection from the extreme cold, often needing specialized systems to minimize thermal bridging. Zones 6, 7, and 8 also require a prescriptive minimum R-value of 13 + 10 ci for 2x4 wood above-grade walls. However, these zones require an R-value of 10 for slabs and crawl spaces, and R-15 for basements.
Using continuous insulation systems such as OX-IS helps to meet or exceed IECC requirements across all climate zones for insulation, particularly in the zones with stricter guidelines. IECC insulation requirements are tailored to the specific needs of each climate zone to ensure energy efficiency, moisture management, and thermal comfort. In hot-humid zones, insulation focuses on managing heat gain and preventing moisture intrusion, while mixed and cold zones prioritize retaining heat during colder months and controlling moisture. Very cold to subarctic zones face the most extreme conditions, necessitating high insulation levels and specialized systems to protect buildings from severe cold to minimize energy loss.
Ready for Any Climate
In a time where extreme weather conditions are becoming more of the norm, selecting the right building materials is more critical than ever.
Climate change continues to reshape our world, so the selection of resilient and high-performance building materials is no longer a luxury, but a necessity. All-weather sheathing stands at the forefront of this conversation, offering a versatile, year-round solution that addresses the unique challenges of different climate zones across the United States. By providing continuous insulation, superior airtightness, and moisture management in a singular product, builders and contractors can achieve IECC standards and create energy-efficient, comfortable spaces year-round. With its ability to reduce heating and cooling costs for the long term, all-weather sheathing proves to be a versatile, cost-effective, year-round performer that is ready for any environment.